금속산화물 나노구조체를 이용한 화학저항식 가스센서의 최신 연구동향
Recent Research Trends for Metal Oxide Nanostructures Based Chemoresistive Gas Sensors
Article information
Trans Abstract
In the modern era, advanced industrial and process technologies in various fields are known to produce harmful gases. These gases typically leak at low concentrations, but continuous exposure can cause serious harm to health and safety. Since human sensory organs cannot detect these risks or leaking hazardous gases, there has been significant interest in developing high-performance gas sensors capable of rapidly detecting harmful and hazardous gas leaks. Metal oxides possess several advantages for such applications, including ease of manufacturing, affordability, and high sensitivity to harmful gases. In this review, we highlight recent progress in the field of chemo-resistive gas sensors based on metal-oxide nanostructures. It begins by discussing the features of various nanostructure morphologies such as 0-dimensional nanospheres to nanocomposites of nanowires. It then describes methods for fabricating metal-oxide nanostructures. Finally, we describe recent advances in the design and fabrication of nanostructures for metal-oxide gas sensors using four different morphologies: 0-dimensional (0 D, nanosphere and nanoparticle), 1-dimensional (1 D, nanowire and nanorod), 3-dimensional (3 D, nanoflower and nanocomposite), and heterojunctions. Based on their morphology-dependent sensing properties, there are various fields of application for gas sensors, with different target gases. This review can serve as an overview of recent research trends and offer insights into the future development of next-generation high-performance gas sensors.
1. 서 론
인간의 삶의 질 및 기대수명이 향상됨에 따라, 개인 건강에 대한 인식의 변화와 관심이 증가하고 있으며, 지구상에 존재하는 모든 생명체에 막대한 피해와 심각한 영향을 줄 수 있는 독성 미세먼지와 대기오염이 사회적 문제로 이슈화되고 있다. 이에 따라, 2019년 세계보건기구(WHO)는 세계 10대 보건 위협 중 대기오염을 첫 번째로 선정하였다[1]. 또한, 현대에 들어 산업 및 공정 기술의 발전으로 인해 다양한 유해 가스가 추가적으로 발생되고 있으며, 일반적으로 낮은 농도로 배출되나 장시간 지속적으로 노출되면 인체에 심각한 피해를 줄 수 있다. 이러한 가스들은 대기의 확산을 통해 건설 및 산업현장 이외에도 대부분의 시간을 소비하는 집, 병원, 학교, 직장 등과 같은 실내 환경에서도 다양한 유해 가스에 쉽게 노출될 수 있다. 인간의 감각기관은 낮은 농도의 무취, 무색의 유해 가스 누출과 위험성 및 누출량을 직접적으로 감지할 수 없으므로, 가스의 누출을 빠르게 감지할 수 있는 고성능의 가스센서의 개발이 필요하다.
가스센서는 1923년 Johnson에 의해 촉매연소식 센서가 처음으로 보고되었으며, 감지하고자 하는 가스의 종류와 동작 방식에 따라 전기화학식, 반도체식, 열도전식, 광이온화식 등 다양한 형태의 가스센서가 개발되고 발전되어 왔다. 그 중에서도 SnO2 [3], In2O3 [4], ZnO [5] 등의 금속산화물을 기반으로 한 반도체식 가스센서는 가스 감지소재의 표면에서 특정 가스에 대한 흡착 및 탈착을 통해 저항 변화를 측정하여 가스 감도, 반응 시간 등을 얻을 수 있는 간단한 동작 방식과 공정의 용이성, 대량생산의 용이성, 소형화, 저 농도의 가스에 대한 고 감응도 등의 장점으로 차세대 가스센서로써 많은 관심을 받고 있다[2]. 하지만, 반도체식 가스센서의 감지소재는 가스의 흡착과 탈착을 위해 고온이 유지되어야 함으로 높은 소비전력의 Heater가 필요하다. 반도체 감지소재 표면에서 가스 분자의 흡착 및 화학적 반응은 활성화 에너지를 요구하는데, 높은 작동온도는 타겟 가스의 흡착/탈착과 가스 확산을 가속화할 수 있는 높은 활성화 에너지를 제공하기 때문이다[7]. 이는 휴대용 기기나 웨어러블 기기, 또는 다종센서의 집적화에는 적용하기 어렵다는 한계점이 존재한다.
이러한 문제를 해결하기 위해서는 귀금속을 금속산화물 표면에 추가로 증착하거나, 다른 물질과의 이종 접합을 통해 밴드 갭에 변화를 주거나 [8], 빛에 의해 활성화를 시키는 등의 방법들이 연구되고 있다[9]. 귀금속을 증착과 이종 접합 방법은 가스센서의 선택성 향상에는 효과적이나, 작동온도를 낮추는 데에는 한계가 있으며, 빛을 이용하여 활성화하는 방법은 센서의 작동온도를 상온까지 낮출 수 있는 장점이 있으나, 가스와의 반응성이 극히 저하되거나 회복이 되지 않는 단점이 있다[10].
최근 기존 금속산화물의 나노구조화를 통하여 기존 한계를 극복하고자 하는 노력이 활발히 진행되고 있다[11]. 금속산화물을 기반으로 한 0차원, 1차원, 2차원, 3차원 나노구조체는 기존 벌크 형태의 감지소재들과 다르게 다양한 전기적, 화학적, 광학적 특성을 보인다. 또한, 나노구조화로 인한 높은 비표면적으로 인해 가스 반응성이 매우 향상되며, 표면 개질과 기능화를 통해 상대적으로 낮은 온도에서도 가스와 반응한다는 연구결과도 보고되고 있다. 이러한 금속산화물 나노구조체는 수열 합성, 열 증착법, sol-gel 법, 전기 방사법, 경사각 증착법, 양극산화 방법 등과 2개 이상의 공정조합으로 제작할 수 있다 [12].
본 논문에서는 0차원, 1차원, 그리고 3차원의 나노구조체에 대한 개요와 금속산화물 나노구조체를 제작하는 방법을 소개하고, 금속산화물 나노구조체를 이용한 고감도, 상온 동작 가스센서 응용과 함께 공정 조합으로 형성된 새로운 감지소재에 관한 최신 연구 동향을 소개하고자 한다.
2. 금속산화물 나노구조체의 개요
2.1 나노구조체 형상제어
2.1.1 0차원 나노구조
나노입자는 일반적으로 1~100 nm의 지름을 가지는 물질의 입자를 정의하며, 매우 작은 입자이기에 매우 높은 비표면적을 가지고 있어 탄소 배출, 촉매 반응, 또는 배터리 충/방전과 같은 표면반응에서 많은 이점이 있다. 이러한 0 차원 나노입자는 합침법, 마이크로파 합성, 또는 수열 합성법을 통해 합성될 수 있다. 함침법은 여러가지 전구체를 용매에 녹여 고온에서 반응시켜 나노입자를 합성하는 방식이며, 마이크로파 합성은 나노입자가 형성될 때 마이크로파에 의해 온도변화를 주는 방법으로 전구체를 포함하는 용액에서 환원율을 급격하게 증가시켜 입자의 형태에 영향을 주게 된다. 마이크로파 온도에 따라 1차원 또는 3차원의 나노구조를 갖기도 한다. 또한, 나노입자는 일반적으로 다른 물질과의 이종 접합이 쉬워 1차원, 2차원 형상의 물질과 복합체를 형성하여 다양한 물리적, 화학적 물성을 가질 수 있도록 설계할 수 있다. 예를 들면, 나노튜브나 나노 선과 같은 1차원 나노구조체에 나노입자를 접합하면 기존 나노 선 구조보다 표면적이 증가하여 높은 감도와 빠른 반응/회복 속도를 가지게 된다[14].
2.1.2 1차원 나노구조
나선형 구조의 나노 선 및 나노로드는 높은 종횡비를 가지고 있어 기존의 다결정 및 벌크한 구조와 다른 물성을 가지며, 금속이외의 비금속 원소를 포함하는 다양한 조성으로 합성이 가능하다. 1차원 나노 선 및 나노로드를 합성하는 방법에는 대표적으로 두 가지 형태가 있다[15]. 하나는 유기 금속 증착법 중 하나인 MOD 법(Metal-Organic Decomposition Method)은 기판에 나노로드가 성장할 수 있는 방향성을 가진 씨앗 층(seed layer)을 형성한 후 수열 합성법을 통하여 성장하는 방법이다. 다른 방법으로는 VLS 법 (Vapor-Liquid-Solid method)이 있다. VLS법은 합성하고자 하는 물질의 전구체를 증발시켜 기체 상태(Vapor)로 만들고, 기체 상태의 전구체가 기판이나 촉매 역할을 하는 입자와 반응하여 액체 상태 (Liquid)가 되어 전구체 물질이 석출되면서 고체 (Solid)로 바뀌게 되는 방식이다. 이렇게 합성된 1차원 나노 선 구조는 2차원 박막 형태의 물질에 비해 표면적이 넓고, 정렬된 형태로 물질을 얻을 수 있어 최근 가스센서 분야에 많이 적용되고 있으며[15,16], 마이크로 단위 전자소자 개발에 사용되어 주로 태양 에너지 변환, 열전 소자[17], 에너지 저장 매체[18] 등으로도 응용되고 있다.
2.1.3 3차원 나노구조
3차원 나노구조체는 한 축으로만 성장이 진행되는 1차원 나노 선과 달리 성장 시작점에서 여러 방향으로 성장이 진행되는 나노 꽃과 같은 형상을 하고 있거나, 나노 선이 고밀도로 군집하여 하나의 큰 단위 밀집구조를 형성하기도 한다. 비규칙적으로 성장하는 1차원 나노 선과 달리 규칙적으로 밀집하여 큰 구조체를 형성하기 때문에, 동일 부피 안에서 더 높은 비표면적을 가지게 되어 높은 가스 감응도를 낼 수 있다는 장점이 있다[19].
3차원 나노구조체를 만드는 방법에는 대표적으로 경사각 증착법과 수열 합성법이 있다. 경사각 증착법은 증착 물질의 플럭스와 증착 기판간 각도를 조절하여 증착하는 방법으로, 경사각의 변화를 통해 형성되는 나노구조체의 공극, 밀도 및 크기를 조절할 수 있다. 수열 합성법은 1차원 나노 선 합성법과 같이 전기방사를 통하여 나노로드로 씨앗층을 먼저 형성시킨 후 수열 합성을 통해 나노구조체를 만드는 방법이다. 수열 합성을 진행할 때 씨앗 층의 형태를 바꿔주게 되면 그에 따라 최종 구조체의 형태가 바뀌게 되는 특징이 있다. 최근 연구에서는, 3차원 나노구조체 위에 다른 소재를 증착하거나 치환반응을 통하여 다른 소재와의 이종 접합을 만들어 가스센서 성능을 향상하는 연구가 이루어지고 있다 [20].
2.2 나노구조체 합성방법
2.2.1 수열 합성 (Hydrothermal method)
수열 합성법은 폐쇄된 환경에서 전구체 수용액을 반응물로 용해해 중/저온, 고압의 조건을 형성하여 원하는 대상 물질로 재결정될 수 있도록 하는 방법이다. 수열 합성은 용액공정이기 때문에, 공정 조건을 제어하기 쉬워, 경제성 있게 우수한 분산력 및 고순도 물질을 얻을 수 있다는 장점이 있어 나노구조체를 합성하는데 가장 일반적인 방법으로 알려져 있다. 특히, 나노구조를 합성할 때 공정변수로서 전구체의 종류와 농도, 합성온도, pH 등의 조절을 통해서 합성물의 결정 형상 및 크기 등을 제어하기 용이하다.
2.2.2 열/ 전자 빔 증착법 (Thermal/E-beam evaporation method)
열 증착법은 물리적 기상 증착법의 일종으로, 증착이 일어나는 챔버 안을 진공으로 만들고 증착하고자 하는 전구체를 가열하여 기체로 증발시키게 되면 맞은 편에 있는 기판에 기체들이 응축되어 증착이 되는 합성 방법이다. 이 방법을 통해 1차원 상의 나노 선, 나노로드와 같은 나노구조체 뿐만 아니라, 2차원 박막 형태의 금속산화물을 Si/SiO2와 같은 기판에 형성시킬 수 있다. 하지만 열 증착법의 경우 균일하고 고품질의 박막을 만들기 위해서는 일반적으로 10-4 Torr 이하의 높은 진공도가 필요하다.
또한, 전자 빔 증착법(E-beam evaporation)은 전자 빔을 이용하여 증착하고자 하는 전구체를 가열하여 증착하는 방법으로, 주로 타겟 물질이 높은 용융점을 가지고 있을 때 사용한다. 자기장에 의해 유도된 전자 빔이 닿은 전구체의 표면부터 증발이 일어나기 때문에, 오염이 적다는 장점이 있다. E-beam evaporation 방법 중, 경사각 증착법은 증착 물질이 증발되는 방향과 증착 기판을 일정한 기울기를 갖도록 설정한 후, 증착 시에 기판 표면의 수직 축을 중심으로 회전을 시켜 물질을 증착하는 방법이다. 공정 초기에는 기판 위에 나노 사이즈의 입자들이 무작위로 생성되며, 이후에는 입자들에 의해 생기는 그림자 효과와 분자의 이동성 제한에 의해 초기에 생성된 입자들의 위에서만 증착이 이루어지며 나노 선 구조가 형성된다. 증착 온도, 경사각 등에 의해 표면적, 공극률, 나노 선의 길이 등이 결정되어 다양한 형태의 나노구조체를 만들 수 있는 장점이 있다.
2.2.3 Sol-gel 법 (Sol-gel method)
Sol-gel법은 용액공정으로 무기 염을 전구체로 사용하고 일련의 화학반응을 통해 용액 내에서 안정하고 투명한 sol 물질을 형성하는 방법으로 저온에서 가열하게 되면 sol이 gel로 변하게 되고 금속산화물 또는 수산화물이 sol에 천천히 침전된다. 이때, gel을 더 높은 온도에서 가열하여 원하는 물질을 얻을 수 있게 된다. 이러한 sol-gel법은 유동학적인 특성에 따라 분무, 침지 및 함침을 통해 나노 단위의 박막을 제조하는 데에 사용되고 있다.
2.2.4 전기방사법 (Electrospinning method)
전기방사 방법은 정전기 조절을 통해 정밀한 나노 섬유를 제조하는 방법이다. 고분자 전구체 용액을 강한 정전기 장을 활용하여 회전 노즐 방사를 통해 전구체 용액이 집진판에 수백 나노미터 단위로 형성된다. 이 방법은 고분자 전구체를 응집시키거나 고온의 소결 방법을 사용하지 않고 나노구조체를 합성할 수 있는 장점이 있으며, 나노 섬유의두께 및 방향을 조절하여 다양한 형태의 나노구조체를 만들 수 있는 방법으로 사용된다.
3. 금속산화물 나노구조체 기반 가스센서 최신 연구동향
3.1 0차원 구조
반응/회복속도의 증가 또는 가스센서의 선택성을 높이기 위해서 금속산화물 나노입자에 다른 나노입자를 접합하거나 나노입자를 형성할 때 구조적으로 공극이나 결함을 조절하는 연구가 진행되고 있다. 그림 1은 2023년 스웨덴 왕립공과대학교에서 발표한 In2O3-graphene@Cu (IG) 가스 센서 물질 합성 및 특성평가에 관한 연구내용이다[21]. Cu(NO3)2와 citric acid를 혼합한 전구체를 연소한 후 In(OH)3겔과 함께 소결하여 IG 나노복합체를 합성하였으며, 합성된 나노복합체는 작은 정육면체의 In2O3 결정이 graphene@Cu flake로 감싸져있는 것이 확인되었으며, graphene@Cu는 소결과정에서 In2O3 결정 성장의 중심이 되어 In2O3끼리 뭉치는 것을 방지해주어 표면적을 증가시켜 전체적인 가스감지 성능에 영향을 미치게 된다. 첨가한 graphene@Cu의 wt%에 따라 4wt% 샘플 (IG4)까지 NO2 가스에 대한 감응도가 비례적으로 증가하다가 6wt% 샘플 (IG6)에서 NO2 감응도가 급격히 감소하는 것을 확인할 수 있다. 6wt% 이상에서는 graphene@Cu와 나노복합체를 형성할 수 있는 In2O3 의 구조적 결함이 포화를 이루게 되면서 active site가 줄어들어 가스에 대한 반응성이 감소하게 된다. 또한, IG 나노복합체는 SO2, CH4, NO2, acetone, ethanol 등 다양한 가스에 대한 반응성도 있음을 확인하였으며, graphene@Cu의 농도가 증가할수록 NO2 가스에 대한 감응도가 증가하는 반면, 다른 가스에 대한 가스 감응도는 낮아졌다.

(a) Schematic illustration of the In2O3-G@Cu powder nanocomposite synthesis and in-situ calcination method. (b-g) TEM images of the synthesized powders of (b) pure In2O3, and In2O3-G@Cu nanocomposites with different weight ratio between In2O3 and G@Cu nanocomposites. (h) Gas sensing response using IG composites for different target gases. (i) Sensing response of IG4 (pure In2O3 with G@Cu 4 wt%) sensor to different target gases at 420 °C. (j) Sensing response of IG4 sensor to gas mixtures with various concentrations of NO2 at 420 °C [21].
한편, 0차원의 일반적인 CeO2 나노입자를 간단한 수열 합성을 통해 나노구조체를 형성하여 CO2 가스센서에 적용시키는 연구가 최근 보고되었다 (그림 2) [22]. 에틸렌 글리콜과 증류수 분위기에서 과산화수소, Ce(NO3)3·6H2O, 그리고 citric acid를 160도에서 수열합성을 통해 yolk-shell 구조의 CeO2를 제작하였다. 해당 연구는 yolk-shell 구조의 CeO2 나노입자와 일반적인 CeO2 나노입자의 CO2 가스센서 성능비교를 통해 구조에 의한 반응성 및 다양한 습도 조건에서의 안전성 향상을 보고하였다. Yolk-shell 구조의 CeO2는 일반적인 CeO2 나노입자와 달리 상대습도 30, 50, 70 %에서도 CO2 가스에 대한 감응도가 유지되는 것을 확인하였다. 또한, 일반적인 CeO2 나노입자의 경우 가스센서로 응용하기에는 기저 저항 회복 (recovery)이 잘 안된다는 한계가 있었으나, yolk-shell 구조의 CeO2 가스센서는 기저 저항까지 잘 되돌아오는 높은 회복성능을 보였으며, 빠른 반응/회복시간과 높은 CO2 가스 감응도를 확인할 수 있었다. 이러한 성능향상은 높은 공극도를 가지는 yolk-shell 구조에 의해 일반적인 CeO2와는 달리 내부에 가스의 확산이 가능해지고 가속화되면서 일어나는 것으로 확인되었다.
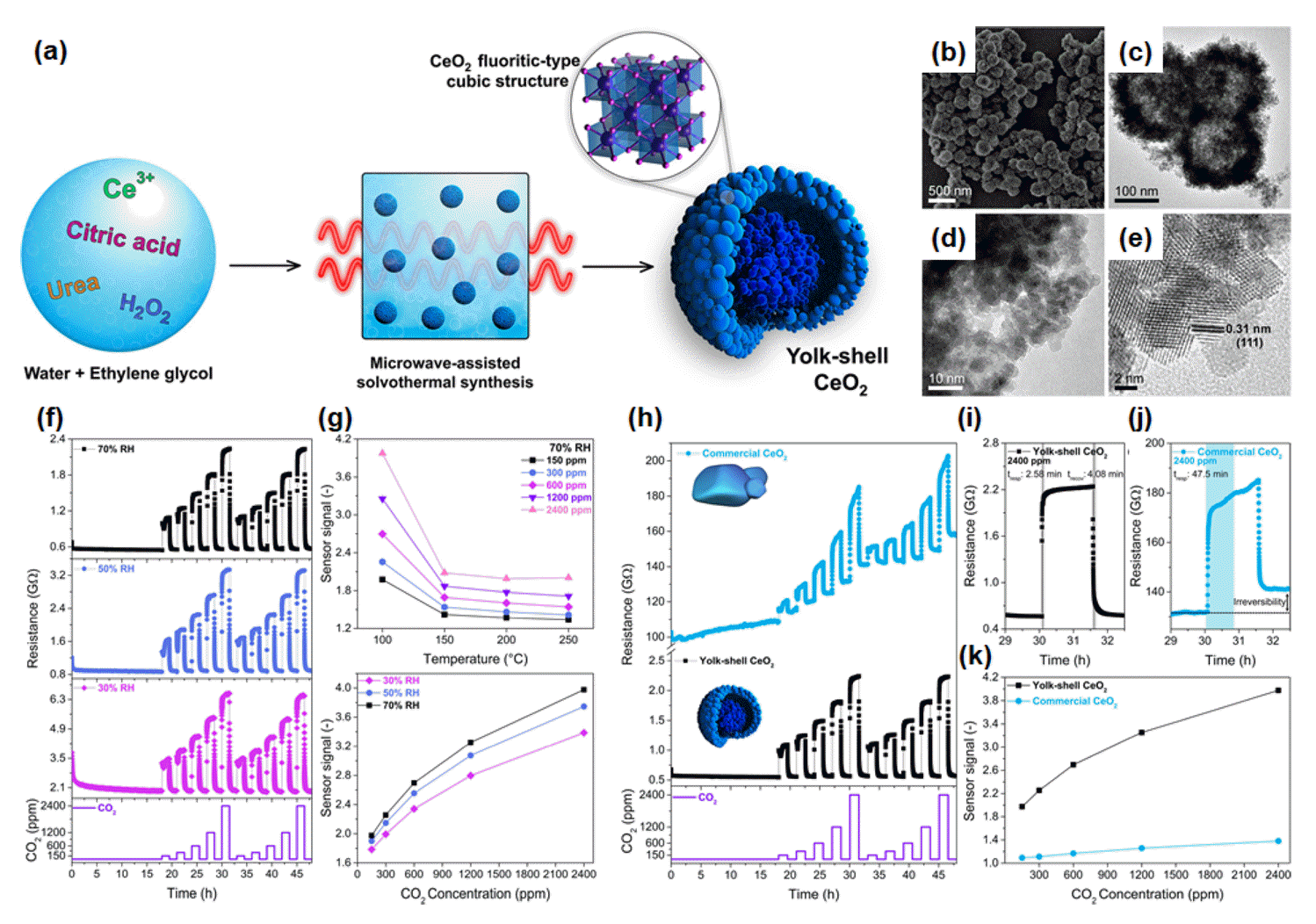
(a) Schematic illustration of the synthesis procedure of yolk-shell CeO2 nanospheres. (b) FE-SEM image, (c) TEM image, and (d, e) HRTEM images of yolk-shell structure of CeO2. (f, g) Gas sensing properties of CeO2 nanosphere gas sensor for CO2 150-2400 ppm with humid air (at 30, 50, and 70% RH). (h) Comparison of resistance changes in both commercial and yolk-shell CeO2 gas sensing channel upon CO2 exposures in the concentration range of 150-2400 ppm. Response and recovery times of the (i) yolk-shell CeO2 nanosphere and (j) commercial CeO2-based gas sensors. (k) Gas response comparison between yolk-shell and commercial CeO2 nanoparticles [22].
3.2 1차원 구조
한국공과대학교에서는 상온 작동이 가능한 NO2 가스센서를 제작하기 위해 ZnO 나노튜브를 TiO2 나노입자와 접합하였으며, 자외선(UV) 영역 파장의 빛을 추가로 조사하여 특성을 향상시키는 연구를 보고하였다(그림 3) [23]. Si wafer 위에 전기방사법을 통해서 PVP 나노로드를 합성하고 RF 스퍼터를 이용하여 ZnO를 증착하였으며, 그 후 Ti을 열 증착법으로 증착한 후 800 °C에서 열처리를 진행하여 PVP 층을 제거하였다. 증착된 Ti층은 열처리를 통해 TiO2 나노입자로 변하고, ZnO 또한 나노튜브 또는 한쪽이 뚫려있는 Hemitube 모양으로 형성된다. ZnO 나노튜브와 ZnO/TiO2 hemitube구조 모두 UV(ultra violet, 자외선)을 조사하기 전에는, NO2 가스를 감지하지 못 하였다. 하지만 UV를 조사한 경우, 상온에서 NO2 가스를 감지하는 것을 확인하였다. 가스센서의 감응도는 금속산화물 내의 자유전자의 수와 관련이 있다. 상온에서는 ZnO의 자유전자가 적기 때문에 낮은 반응성과 긴 반응/회복시간이 나타나고, UV 빛을 조사하게 되면 광여기를 발생한 광전자로 인해 가스의 흡착/탈착 반응에 참여할 수 있는 자유전자의 수가 증가하게 되어 감응도가 증가한다[24]. 또한, ZnO 나노튜브보다 ZnO/TiO2 hemitube가 회복이 잘 되는 것을 볼 수 있었는데, 이는 hemitube구조가 나노튜브 구조보다 산소 이온이 더 쉽게 흡착/탈착이 이루어지기 때문이다. Hemitube구조가 더 많은 산소 공공에 의한 결함이 더 많으며, 이로 인해 더 많은 가스 분자의 활성 영역이 증가하기 때문에 높은 감응성을 보인다는 것을 보고하였다.
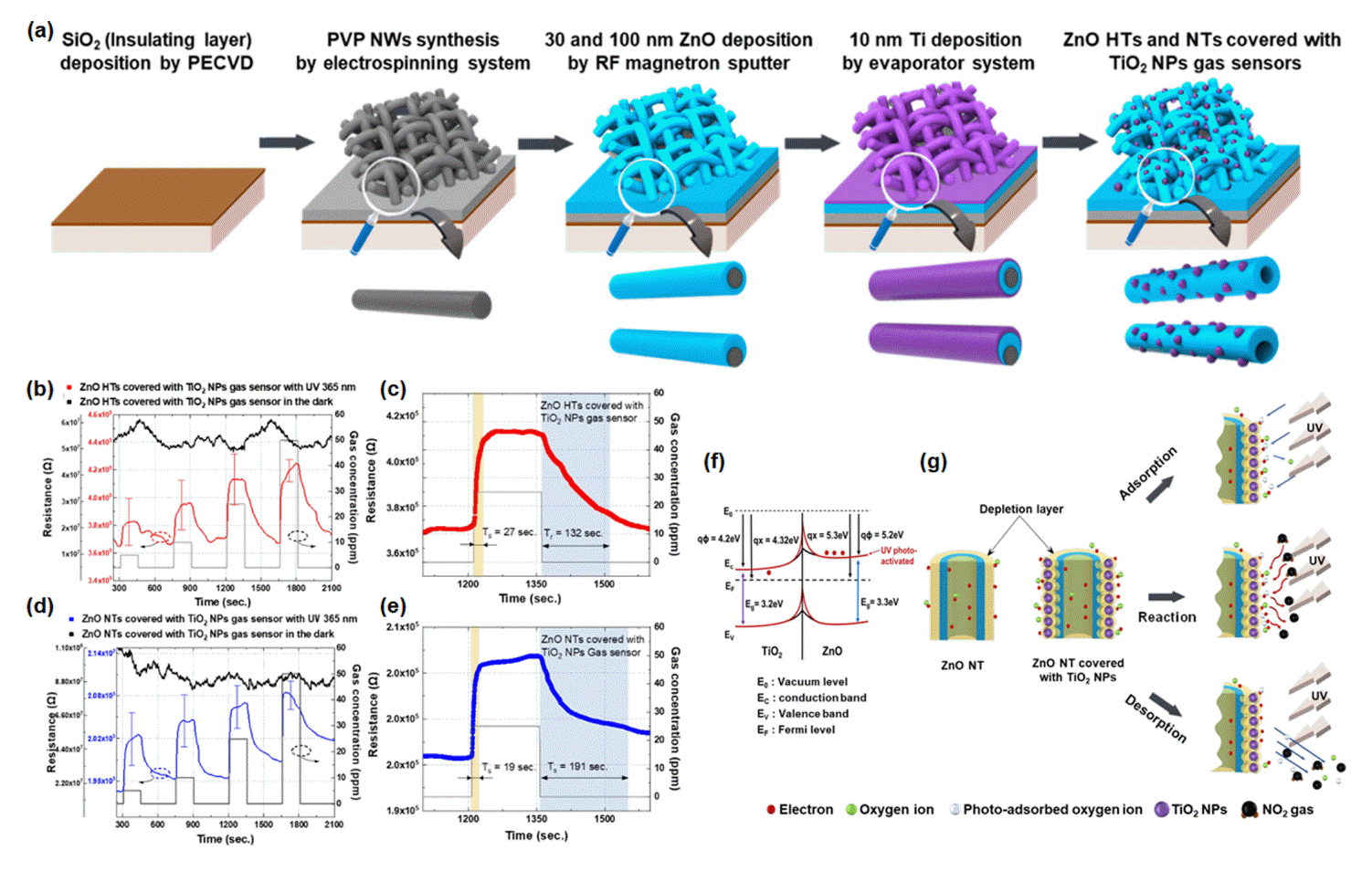
(a) Fabrication procedure for gas sensors consisting of ZnO hemitubes (HTs) and nanotubes (NTs) covered with TiO2 nanoparticles (NPs). (b) Resistance of ZnO HTs covered with TiO2 NPs gas sensor in response to different NO2 concentrations with and without UV illumination, (c) resistance of ZnO HTs covered with TiO2 NPs gas sensor to 25 ppm of NO2, (d) resistance of ZnO NTs covered with TiO2 NPs gas sensor in response to different NO2 concentrations with and without UV illumination, and (e) resistance of ZnO NTs covered with TiO2 NPs gas sensor to 25 ppm of NO2. (f) Ideal band structure and electron transfer between ZnO and TiO2. (g) Schematic diagram of the possible gas sensing mechanism of photoactivated ZnO NTs covered with a TiO2 NPs [23].
한편, 공주대학교에서는 국부적인 수열합성을 통해 ZnO 나노로드를 금(Au) 전극 위에 합성하고, 팔라듐(Pd)을 열증착법을 통해 ZnO 나노로드 위에 추가로 증착하여 가스 센서를 제작하였다. 그 후 표면 황화처리를 통해 Pd/ZnS/ZnO의 이종접합 구조를 가지는 황화수소(H2S) 가스센서 소자를 제작하는 방법에 대하여 보고하였다(그림 4) [25]. Pd 나노입자의 증착 유무에 따라 H2S 가스 감응도가 H2S 의 농도가 10 ppm일 때 631 %에서 4491 %까지 증가하는 것을 확인할 수 있었으며, Pd 나노입자가 도포됨에 따라 H2S 10 ppm에 대하여 반응시간이 90초에서 61초까지 줄어들었고, 회복시간은 229초에서 62초로 줄어들어 성능이 향상됨을 확인하였다. 이러한 성능향상은 Pd 나노입자가 촉매로써 작용되어 표면에서 일어나는 흡착/탈착의 활성화 에너지를 낮추기 때문에 표면 반응이 활성화되어 나타난다. 또한 CO가스를 제외한 아세톤, 에탄올, 톨루엔 가스에서도 감도의 향상을 확인하였지만, H2S에 대한 매우 높은 선택성이 관찰되었다.
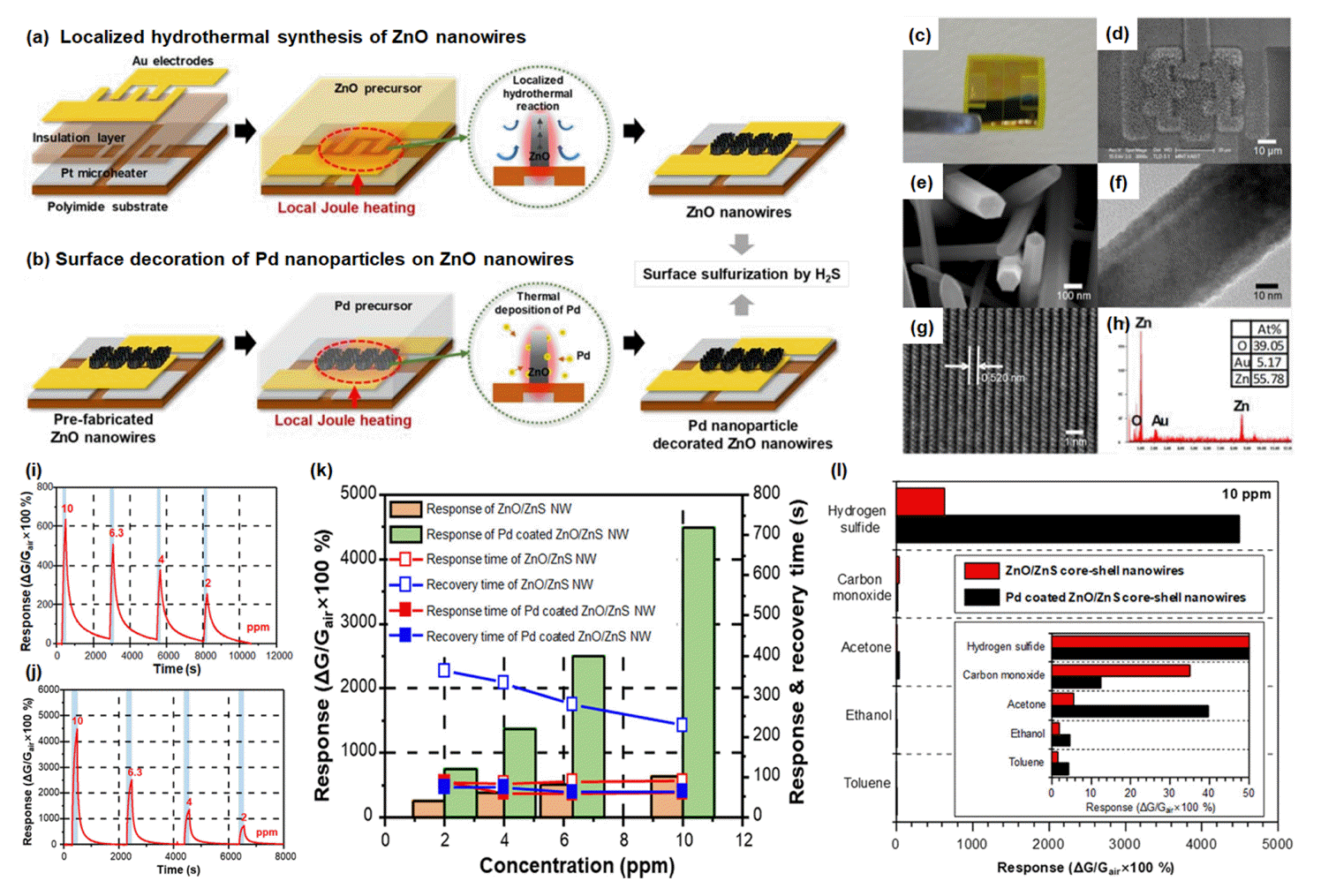
Schematic illustrations of (a) pristine zinc oxide (ZnO) nanowire synthesis process on a polyimide (PI) substrate via local heating and (b) palladium (Pd) nanoparticle coating process on the surface of ZnO nanowire via local heating. (c) Photograph and (d) SEM image of flexible sensor device. (e) SEM image of ZnO nanowires. (f, g) TEM images and (h) energy dispersive x-ray spectroscopy (EDS) data of ZnO nanowire. (i) Dynamic gas sensing response of (i) ZnO/ZnS core-shell nanowires and (j) Pd nanoparticle decorated ZnO/ZnS core-shell nanowire under H2S gas. (k) Comparison of response, response time and recovery time vs. H2S concentration between ZnO/ZnS core-shell nanowires and Pd nanoparticle decorated ZnO/ZnS core-shell nanowires. (l) Gas selectivity test of ZnO/ZnS-based gas sensing channel using various toxic gases [25].
3.3 3차원 구조
서울대학교에서는 Pt-IDE(platinum-interdigitated-electrode) 전극 위에 나노패터닝을 통해 3차원 구조의 TiO2를 제작하였으며, 이를 통해 고성능 아세톤 가스센서에 적용하는 연구를 발표하였다 (그림 5) [26]. PS bead와 photoresist를 이용한 구조체 합성을 통해 템플릿을 제작한 후 atomic layer deposition(ALD)로 TiO2층을 증착하고, 열처리를 통하여 PS bead를 제거하여 3차원의 TiO2 나노구조를 형성하였다. 3차원의 TiO2 나노구조체의 TiO2 shell의 두께가 증가함에 따라 기저저항이 감소하는 것을 확인하였으며, TiO 2 shell의 두께가 70 nm일 때 아세톤 가스에 대한 반응성이 기존 TiO2 박막에 비해 약 169배 증가되었다. 또한 400 °C에서 3차원 TiO2 나노구조 기반 가스센서의 아세톤 감지 성능을 평가하였을 때, 기존 박막 형태보다 반응성이 약 299배 증가된 성능을 보였다. 가스 반응성에서의 성능 향상은 3차원의 TiO2 구조체가 되면서 발생한 높은 공극도로 인해 타겟 가스가 구조체 하단의 기판 및 전극까지 쉽게 도달할 수 있게 되었기 때문이다. 높은 공극도를 가지는 나노구조에 의해서 얇은 껍질 구조의 산화층 표면이 가스 감지반응에 참여하게 되어 성능 향상이 일어남을 보고하였다.

Fabrication and structural analysis of 3D TiO2. (a) Photograph and schematic illustration of direct-fabricated 3D TiO2 nanostructures on interdigitated electrodes (IDEs). (b) Cross-sectional STEM image and (c) magnified STEM image of 3D TiO2. (d) XRD spectra of 3D TiO2. (e) HR-TEM image of 3D TiO2. Inset is a selected area diffraction (SAED) pattern in a fast Fourier transform (FFT) image. (f) Energy dispersive spectroscopy (EDS) mapping of Ti and (g) O for 3D TiO2. (h) gas response curves and gas response (red) and base resistance (blue) for 3D TiO2 with different TiO2 shell thickness (30, 50, 70, and 100 nm) at 400 °C. (i) Gas response curve and gas responses (red) and base resistances (blue) for 3D TiO2 with 70 nm shell thickness at different operating temperature (200, 250, 300, 350, 400, and 450 °C.) (j-k) The gas sensing mechanism of 3D TiO2 toward CH3COCH3, Schematic illustrations of (j) gas molecule accessibility depending on TiO2 nanostructures and (k) depletion formation at the internecks between TiO2 ellipsoid cores and resulting current level upon exposure to CH3COCH3 gas. [26].
또한, 서울대학교에서 경사각 증착법을 통해 NiO와 Co3O4이 접합된 나노구조체를 제작하여 휘발성 유기 화합물들(VOCs)에 높은 반응성과 선택성을 가진 가스센서에 대한 연구를 발표하였다 (그림 6) [27]. Pt-IDE 전극 위에 Ni과 Co3O4 를 73, 75, 78, 80, 83도의 경사각으로 80 rpm의 속도로 회전시키며 e-beam 증착하여 나노구조체의 밀도와 두께가 다르게 증착 됨을 확인하였다. 이렇게 제작한 3차원 나노구조체의 증착 경사각, 작동온도, Ni의 증착 두께에 따라 에탄올 가스에 대한 반응을 확인하였다. Co3O4 나노구조체의 증착 경사각이 75도일 때 가스 감응성이 가장 높았으며, 작동온도가 350 °C일 때 가스 감응성이 가장 높았다. 또한 Ni의 증착 두께에 대해서는 NiO의 두께가 1 nm일 때 가장 높은 저항변화를 보였으며, 75도 이상의 경사각 증착 샘플의 반응성이 감소하는 것은 증착된 나노 선 사이의 거리가 75도까지는 감소하다가 그 이후로는 증가하여 전기적으로 전도할 수 있는 통로가 적어지는 것으로 보고하였다. 그리고 휘발성 유기 화합물들에 대한 가스 감응 특성을 관찰하였는데, Co3O4으로만 이루어진 3차원 나노구조체에서는 에탄올에 대하여 가장 높은 반응성을 가지고 다음으로는 아세톤, 아세트알데히드 가스 순서로 반응성이 높은 것을 확인하였다. 하지만 니켈을 함께 증착시킨 구조체에서는 거의 모든 가스에서 4배 이상 가스 감응성이 증가한 것을 확인하였다. 하지만, 에탄올, 에탄올 가스 순서로 높은 반응성을 보이는 것으로 확인하였으며, 특히 벤젠에 대해 높은 선택성(약 17배)을 가지는 것을 보고하였다. 이러한 VOCs에 대한 반응성 향상은 1) 격자 구조의 변화에 의한 활성 사이트의 증가, 2) p-p타입 이종 접합 구조로 인한 흡착 시의 반응 안정성 증가, 3) 수직적으로 정렬된 나노구조 형성에 의한 표면적 증가, 4) NiO의 촉매효과에 의한 복합적인 결과임을 보고하였다.

Schematic illustration of initial nucleus formation at different incident angles. Cross-sectional SEM images of the bare Co3O4 NRs deposited at (b) 73°, (c) 75°, (d) 78°, (e) 80°, and (f) 83°, and (g) the plain Co3O4 thin film. Inset show plane-view SEM images of each sample. Response transients and response of the bare Co3O4 NRs (h, k) deposited at different angles (73°, 75°, 78°, 80°, and 83°) at 300 °C to three consecutive exposure of 50 ppm C2H5OH and (i, l) measured at different temperatures from 100 °C to 400 °C to 50 ppm C2H5OH. (j, m) Response transients and response of NiO-decorated Co3O4 NRs with different thickness (1, 3, 5 nm) of Ni film at 350 °C to 50 ppm C2H5OH. Response transients of the (n) bare Co3O4 NRs and (o) NiO-decorated Co3O4 NRs to various gases (50 ppm) at 350 °C. Polar plot for (p) responses, and (q) selectivity to various gases (50 ppm) at 350 °C [27].
3.4 이종접합 구조
경사각 증착법을 이용하여증착한 SiO2 나노로드에 MoS2를 접합하여 기존보다 낮은 작동온도인 100 °C에서 작동하는 NO2 가스센서에 대한 연구가 보고되었다. (그림 7) [28]. Pt-IDE가 증착된 Si/SiO2 기판에 경사각 증착법을 통해 SiO2 나노로드을 증착하고 나서 그 위에 (NH4)2MoS4 액상의 전구체를 스핀코팅을 하고, 그 후에 화학기상 증착법(CVD)을 통해 황을 증발시키며 열처리를 진행하게 되면 SiO2 나노로드 위에 MoS2가 접합된 형태의 이종접합 구조 (SiO2/MoS2)의 나노구조체를 형성하게 된다. 이렇게 제작된 SiO2/MoS2 나노구조체를 다양한 작동온도와 가스농도 조건에서 NO2 가스에 대하여 측정한 결과 상온 근처온도 (RT, 50 °C)에서 가장 높은 반응도를 보여주지만, 초기 저항으로의 회복까지 시간이 오래 소요되고 약 50% 정도까지 회복되는 것을 확인하였다. 하지만 작동온도를 100 °C로 올리게 되면 상온에서의 반응성보다 75 % 감소하게 되나, 초기 저항으로 완전히 회복되는 것을 확인하여 측정 온도에 따른 반응성과 저항 회복에 상관관계가 있는 것을 보고하였다. 박막형태의 MoS2 가스센서와 비교했을 때, 약 90배 높은 성능향상을 보였다. 이는 다공성의 1차원 SiO2 나노로드에 MoS2가 수직 방향으로 정렬되었기 때문인데, 가스를 흡착/탈착할 수 있는 active site인 grain boundary의 증가와 반응에 참여할 수 있는 표면적이 증대되었기 때문으로 보고하였다.

(a) Schematic illustration of fabrication process of SiO2 nanorods (NRs) encapsulated by MoS2. Cross-sectional TEM images of the (b) 120-, (c) 250-, and (d) 500nm-thick SiO2 NRs encapsulated by MoS2. (e) EDS mapping images of the SiO2 NRs encapsulated by MoS2. (f) Response transients, (g) response (red, left) and recovery (blue, right) of the SiO2 nanorods encapsulated by MoS2 (500nm MoS2) to 50 ppm NO2 vs. operating temperature. (h) Response transients of the SiO2 nanorods encapsulated by MoS2 (500MoS2) to 3 pulses of 50 ppm NO2 at room temperature and 100 °C. (i) Response transients of the SiO2 nanorods encapsulated by MoS2 toward 1-5 ppm NO2. Inset in (i) show the calibration for the response as function of NO2 concentration. Schematic illustration of (j) the plane MoS2 on flat Pt-IDE/SiO2/Si substrate and (k) the SiO2 NRs encapsulated by partially vertical aligned (edge site exposed) MoS2. The gas adsorption and desorption in vertically aligned MoS2 is more reactive than plane MoS2 [28].
한편, 화중과기대학교에서는 수열 합성법을 통해 ZnO 나노로드를 합성하고 광 증착법(photodeposition)으로 은(Ag) 나노입자와 이종 접합 구조 집합체를 합성하여 NO2 가스센서의 성능향상에 대한 연구를 발표하였다 (그림 8) [29]. Zn을 포함하는 전구체를 전기방사법을 통해 기판 위에 씨앗층을 형성시키고 이를 수열 합성법을 통하여 ZnO 나노로드 집합체를 형성한다. 그 후에 광 증착법에 의해서 ZnO 표면에 Ag 나노입자를 접합하여 이종 접합 구조를 형성하고 ZnO층의 구조에 따라 최종 나노구조체의 구조와 Ag 나노입자의 밀도가 달라진다. Ag 나노입 자의 증착 시간에 따라 합성된 Ag/ZnO 나노집합체를 이용하여 NO2 가스에 대한 가스센서 특성을 측정하였다. Ag 나노입자를 30분 동안 증착한 샘플이 가장 높은 가스 감응도(~14700 %) 를 보였는데, 기존의 ZnO 나노로드 집합체 (~3300 %) 와 비교하여 약 5배 높은 가스 감응 특성을 확인하였다. Ag 나노입자가 가스 흡착의 촉매역할로 작용하게 되어 ZnO 표면에 산소와 NO2 가스의 흡착이 용이하게 만들어 주고, 흡착된 산소 분자의 전자는 Ag의 전도대에서 상대적으로 낮은 ZnO의 전도대로 쉽게 이동하게 되어 가스 반응성이 급격하게 향상된 것으로 보고하였다.

(a) Schematic illustration of fabrication process for Ag-ZnO nanoarrays (NAs), and the optical images of nanowire template, FESEM image of nanowire, and FESEM images of ZnO nanorods and Ag-ZnO nanorods. (b) The schematic oblique and sectional views of NO2 absorption of ZnO nanorod arrays from (I) film-like, (II) ribbon-like, and (III) nanowire-like precursors, respectively, and FESEM images of various ZnO-Nas grown on film-like, ribbon-like and nanowire-like seed layers, respectively. (c) Dynamic response of pure ZnO and Ag-ZnO samples in different NO2 concentrations. The inset of figure (a) is the baseline of samples. Gas response of (d) the pure ZnO and (e) the Ag-ZnO sensors to different concentrations of NO2 at the same working temperature. (f) The chemical sensitization mechanism of catalytic property for Ag-NPs on ZnO nanorods [29].
4. 결 론
대기 오염 문제가 불거지고 개인의 보건에 대한 인식이 개선됨에 따라 휴대가 가능하며, 낮은 작동온도에서 고감도를 가지는 가스센서에 대한 수요가 증가하고 있다. 금속 산화물 기반의 반도체식 가스센서는 대량생산, 소형화, 간단한 작동방식 등의 장점이 있으나, 안정한 소자구동 및 높은 가스감지 특성을 위해 높은 온도의 작동온도가 필요하다. 이러한 문제를 해결하기 위해서, 최근 나노구조체를 활용하여 기존 금속산화물 박막 기반 가스센서의 단점인 높은 작동온도, 느린 회복속도, 낮은 가스 감지 특성을 해결하고자 하는 연구가 보고되고 있다. 0차원, 1차원, 3차원 등의 나노구조체를 형성하여 가스 흡착 비표면적을 증가시키는 것으로 반응성을 높이거나, 다른 전도대를 가진 물질과의 이종 접합을 통해 물성적으로 반응속도와 회복속도를 높여 가스센서의 성능을 향상시키는 연구가 활발히 보고되고 있다. 지금까지 소개한 연구들을 요약하면 표 1과 같다. 금속산화물 나노구조체는 저렴한 제작비용으로 소형화가 가능할 뿐만 아니라, 높은 비표면적을 통한 높은 가스 감응성, 0차원 나노입자부터 3차원 나노복합체까지 필요에 따라 형상을 제어할 수 있다는 장점을 가지고 있어 금속산화물의 태생적 한계를 돌파할 수 있는 방법일 것이다. 다양한 금속산화물 나노구조체를 개발하여 소자 소형화, 높은 가스 감응성, 낮은 동작온도 등의 문제를 해결한다면 소형 휴대용 가스센서, 웨어러블 센서, 저전력 고성능 가스 센서를 구현할 수 있을 것으로 예상된다.
Acknowledgements
이 연구는 과학기술정보통신부가 자금을 지원하는 한국연구재단(NRF)을 통해 국립재료연구데이터센터(NCMRD)의 지원(NRF-2021M3A7C2089748, NRF-2023M3H4A6A01057923)과 전남대학교 학술연구비(과제번호: 2023-0509)지원을 받았습니다.