동적재료모델을 활용한 STS 321 스테인리스강의 고온성형성 평가와 초기 미세조직의 영향
Effect of Initial Microstructure on the High-Temperature Formability of STS 321 Alloy Using a Dynamic Material Model
Article information
Trans Abstract
General austenitic stainless steel has a problem with intergranular corrosion due to volatilizing chromium, which forms chromium carbide in a high temperature environment. By adding titanium as an alloying element, STS 321 stainless steel has excellent creep resistance and intergranular corrosion resistance at high temperatures, because the formation of chromium carbide is suppressed. It is important to find the optimal process conditions for STS 321 stainless steel used in the aerospace field, because high temperature processing is mainly applied, and defects or inhomogeneity of materials that occur during high temperature processing lowers the yield of products. In this study, to investigate the effect of the initial microstructure on the high-temperature deformation behavior of STS 321 stainless steel, a high-temperature compression test was performed on two types of STS321 alloys with different initial microstructures. The temperature range was set at 50°C intervals from 800°C to 1100°C, and the strain rate was set at 10-1/sec intervals from 1 × 100/ sec to 1 × 10-3/sec. Based on the experimental results, the thermal activation energy, which differed depending on differences in the initial microstructure, was calculated. In addition, by deriving flow stress and processing maps, the difference in energy dissipation efficiency depending on temperature and strain rate was explained, along with the initial microstructure and high-temperature deformation mechanism.
1. 서 론
높은 출력 대비 가벼운 엔진의 개발은 우수한 성능의 항공기에서 필수적인 요소이다[1]. 엔진 시스템에 적용되는 소재는 고온, 고압의 환경에 노출되며 이에 따라 비강도가 우수하고 내열성이 뛰어난 소재의 개발이 대두되고 있다[2]. 주로 타이타늄 또는 니켈 기반의 내열합금들이 많이 사용되고 있지만 높은 가격과 용접성 및 가공상의 문제 등으로 인하여 스테인리스강도 사용되고 있다. 일반적인 스테인리스강은 고온의 환경에서 크롬의 휘발 및 크롬 카바이드를 형성하여 입계 부식의 문제를 가지고 있기 때문에 STS 316L, STS 321, STS 347, STS 348 등의 스테인리스강이 사용되고 있다[3,4]. 이 중 STS 321 스테인리 스강은 304 스테인리스강에 합금원소로 타이타늄을 첨가한 것으로 크롬 카바이드의 형성을 억제, 고온에서의 입계부식 저항성을 가지며 크리프 저항성이 우수하다. 또한 일반적인 304, 304L 스테인리스강이 426°C 정도의 환경까지 사용할 수 있는 반면에 STS 321 스테인리스강은 816°C의 온도까지 사용이 가능하다[5].
우주 항공 분야에 사용되는 STS 321 스테인리스강은 주로 고온 가공법이 적용되고 고온가공에 있어 공정중 발생하는 재료의 결함이나 비균질성은 생산품의 수율을 떨어뜨려 생산단가를 높이게 되므로 최적의 공정조건을 찾는 것이 중요하다. 또한 고온 변형에 있어 재료의 적층결함 에너지는 미세조직 형성에 큰 영향을 미치는 것으로 알려져 있다[6]. 높은 적층결함 에너지를 가지는 재료는 열간 성형시, 전위의 상승이 활발해지고 이에 따라 동적회복, 불연속 동적 재결정 거동을 보인다고 보고되고 있고, 낮은 적층결함 에너지를 가지는 재료는 전위의 상승이 어려워지고 변형 중 가공경화 속도의 증가와 함께 동적 재결정이 더 쉽게 일어난다고 알려져 있다[7-11]. 따라서 공정 변수 제어를 통한 미세조직의 제어는 완제품의 물성에 큰 영향을 미치므로 제반 지식으로써 원소재의 초기 미세조직에 대한 이해가 수반되어야 하고 원소재의 합금원소, 가공 정도에 의해 as-received 합금의 초기 미세조직이 변화되고, 이에 따른 소재의 재결정 온도, 고온 변형 기구 등을 파악하여 공정 조건을 설계해야 가공품의 최적의 성능을 이끌어낼 수 있다[12,13].
본 연구에서는 초기 미세조직이 STS 321 스테인리스강의 고온 변형 거동에 미치는 영향을 알아보기 위해 서로 다른 초기 미세조직을 가지는 두 종류의 STS321 합금에 대하여 고온 압축 실험을 수행하였다. 또한 이를 바탕으로 동적재료모델과 여러 불안정 기준을 활용하여 변형공정지도를 작성하였으며 이를 이용해 소성변형유동의 안정 및 불안정 공정 조건을 분석하였다[14-17]. 또한 변형속도에 따른 미세조직학적 변화와 고온 변형 기구, 기계적 특성들을 고온 소성변형거동과 상호 연계하여 이해하고, 최적의 고온 단조성형 조건을 제시하고자 하였다.
2. 실험 방법
본 연구에서는 초기 미세조직이 고온 변형 거동에 미치는 영향을 파악하기 위해 세아창원특수강에서 제조된 Φ40와 Φ500의 직경을 가지는 두 종류의 STS 321 스테인리스강을 사용하였고 시험에 사용된 강재의 조성을 Table 1에 나타내었다. 두 강재의 기본적인 물성을 평가하기 위하여 미세조직 관찰, 상온 인장 시험, 비커스 경도를 측정하였다. 미세조직의 관찰은 시편을 핫 마운팅 하여 #220~#2000의 연마지와 6 μm, 3 μm, 1 μm 연마제, 콜로이드 실리카를 이용하여 경면까지 미세 연마한 후 HNO3 10 ml, HCl 15 ml, CH3COOH 10 ml 혼합액에 부식하여 광학현미경(Optical Microscope, OM, BX53M, Olympus)을 통해 관찰하였다. 경도시험은 비커스 경도 시험기(Vickers Hardness, HM-200, Mitutoyo)를 이용하여 15초의 유지 시간 동안 0.5 kgf의 하중을 가하여 각 시편당 20point씩 경도값을 측정하였고 평균과 표준편차를 계산하였다. 인장시험은 ASTM E8M -16a의 규격에 따라 그립부 Φ10, 표점거리 24 mm 측정부 직경 Φ6의 인장시편 규격으로 가공하여 만능재료시험기(UTM, BESTUM-10MD, Ssaul Bestech)를 통해 1 × 10-3/sec의 변형률 속도로 각 소재별 3회 인장시험을 진행하였다.
초기 미세조직이 고온성형성에 미치는 영향을 알아보기 위하여 고온압축시험기(High temperature compression testing machine, Gleeble3500, Gleeble System)를 통해 고온압축변형시험을 수행하였다. 압축시편은 Φ10 × 15 mm의 크기로 가공하였으며 Φ40 STS 321의 경우 봉재의 단면당 5개씩 길이 방향의 수직으로 채취하였고 Φ500 STS 321의 경우 중심선을 지나도록 4등분 절단한 후 반지름의 중간 지점에서 시편을 채취하였다. 고온압축시험은 800°C~1200°C 온도영역에서 50°C 간격으로 총 8개의 온도 조건(800°C, 850°C, 900°C, 950°C, 1000°C, 1050°C, 1100°C, 1200°C)과 4개의 변형률 속도 조건(1 × 100/sec, 1 × 10-1/sec. 1 × 10-2/sec, 1 × 10-3/sec)에 따라 진행하였다. 각 시편의 시험은 Ar 분위기의 챔버 내에서 승온 속도는 10°C/min, 유지 시간은 1분, 냉각은 공냉 방식으로 수행하였다. 고온 압축 시험 후의 미세조직을 비교 분석하기 위하여 시편을 단면 방향으로 절단한 후 앞서 초기 미세조직을 관찰한 시편과 동일한 방법으로 경면까지 미세 연마한 후 부식하여 광학현미경을 통해 관찰하였다.
3. 결과 및 고찰
3.1 기초물성 비교
서로 다른 직경을 가진 STS 321 스테인리스강의 초기 미세조직 관찰 결과를 Fig 1에 나타내었다. Φ40의 직경을 가지는 강재의 평균 결정립 크기는 17.7 μm를 나타내었고 Φ500의 직경을 가지는 강재의 경우 66.7 μm의 평균 결정립 크기를 나타내었다. 이는 두 강재의 직경에 따른 초기 변형량의 차이 때문이다. 그리고 두 강재 모두 첨가된 Ti가 강재 내부의 N과 결합하여 나타나는 TiN 개재물이 관찰되었는데 미세조직의 차이와는 별개로 TiN 개재물의 크기는 수μm로 동일하였다.

Optical micrograph of as-received STS 321 stainless steel used in the present work (x200); (a) Φ40 diameter, (b) Φ500 diameter.
두 강재의 미세조직의 차이는 기계적 물성에도 영향을 끼치는데, 비커스 경도 시험 결과를 Fig 2에 나타내었다. 직경 Φ40 강재의 비커스 경도는 평균 192 Hv, 표준편차 11.6 Hv를 나타내었고 직경 Φ500 강재는 평균 145.2 Hv, 표준편차 6.39 Hv를 나타내었다. 상온 인장 시험 결과 Φ40 강재의 최대인장강도는 631.6 MPa, 연신율은 72.3%로 나타났으며, 최대인장강도 567.5 MPa, 연신율 66.7%를 나타낸 Φ500 강재 대비 더 높게 측정되었다. 이는 초기 변형량의 차이에 의해 상대적으로 더 미세한 평균 결정립 크기를 가지는 Φ40 강재에서 전위의 이동을 방해하는 결정립계, 전위 등의 결함이 더 많기 때문에 높은 경도, 높은 인장강도 및 연신율을 나타낸 것이다.
3.2 열적 변형 활성화 에너지
고온 변형 시 일어나는 금속 원자의 이동은 가해지는 에너지가 열적 변형 활성화 에너지 장벽 이상일 때 수월하게 진행된다. 열적 변형 활성화 에너지는 고온 압축 시험을 통해 얻어진 유동응력곡선(Flow Stress Curve)으로부터 얻어낼 수 있다. 고온 변형 시 재료의 유동응력은 여러 이론 및 경험식들에 의해 표현될 수 있고[18-20] 이 중 Sellar, Tegart 등[19]은 하이퍼볼릭사인 방정식을 이용하여 다음 식 (1)과 같이 표현하였다.
(A, B: 상수, n: 응력지수, Q: 활성화 에너지)
식 (1)의 양변에 로그를 취한 후 양변을 1/T로 편미분 하면 열적변형 활성화 에너지를 다음 식 (2)과 같이 표현할 수 있다.
식 (2)에서 알 수 있듯이 열적 변형 활성화 에너지는 변형률 속도-역 온도 평면 위의 기울기 값으로 나타날 수 있다. 이를 위해 유동응력곡선에서 변형률 속도에 따른 응력 변화를 조사하였고 이를 바탕으로 변형률 속도-역 온도 그래프를 Fig 3에 나타내었다. Fig 3(a)는 Φ40 강재의 유동응력 곡선과 역 온도 곡선을, Fig 3(b)는 Φ500 강재의 유동응력 곡선과 역 온도 곡선을 나타내며 이를 바탕으로 계산한 열적 변형 활성화 에너지를 Fig 4에 나타내었다. 실제 단조성형 시 소성변형률에 근접한 진변형률 0.6인 조건에 계산된 활성화 에너지 Q는 Φ40 강재에서 평균 365.19 kJ/mol로 측정되었으며 Φ500 강재에서는 평균 252.39 kJ/mol을 나타내었다.
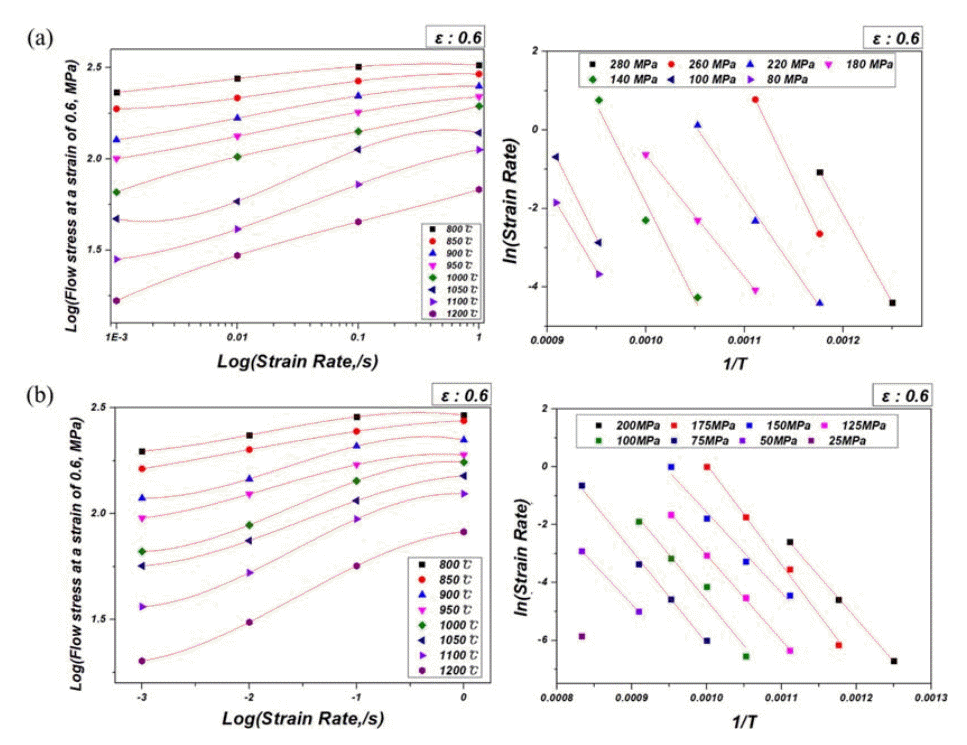
Flow stress curves at different temperatures as a function of strain rate (ε = 0.6) and ln(strain rate) variation as a function of inverse temperature; (a) Φ40 diameter STS 321, (b) Φ500 diameter STS 321.

Thermal activation energy at the various true plastic strain; (a) Φ40 in diameter STS, (b) Φ500 in diameter STS 321.
Φ40 강재에서 더 높은 열적 변형 활성화 에너지가 계산되었는데 이는 열적 변형에너지에 의해 이루어지는 원자간 이동에서 초기에 소성변형을 더 많이 받은 Φ40 강재가 잔류응력, 결정립계 등의 원자간 이동을 방해하는 내부 결함이 더 많기 때문이다. 초기에 변형이 인가된 Φ40 강재에서 더 높은 활성화 에너지 값이 도출되고, 그 이후 동적 재결정 등을 통한 연화현상에 따라 더 낮은 온도조건에서 높은 에너지 분산 효율을 보인다. 그리고 두 강재 모두 진변형률 0.2 이하의 초기 변형 구간에서 나타나는 활성화 에너지가 높게 요구되고 이후 평균값에 수렴하는 양상을 나타내었는데 이는 변형 초기의 원자간 이동에 의한 소성변형에는 더 많은 활성화 에너지가 요구되는 반면, 일정량 이상의 소성변형이 발생한 이후에는 재료 내부의 일에너지가 열에너지로 변환되어 나타나는 소성변형열에 의해 원자 단위의 이동이 더욱 용이해져 더 적은 활성화 에너지로도 충분히 소성변형이 발생하기 때문이다.
3.3 최적의 성형조건 고찰
본 연구에서는 STS 321 스테인리스강의 고온성형성을 고찰하기 위한 모델로 동적재료모델(dynamic materials model) [21]을 기반으로 다항식을 활용하였다. 이 모델에서 재료의 변형시 소모되는 에너지는 주어진 온도와 변형률 속도에 변형을 받았을 때 열로써 분산되는 G와 미세조직학적 변화에 소모되는 에너지 J로 분산된다. 따라서 소성변형동안 재료에 흡수된 총 에너지는 다음 식 (3)과 같이 표현될 수 있다[21].
J 값은 가해진 총 에너지 중 소성변형 시 재료의 미세조직 변화에 관여하며 동적회복 및 재결정, 변형응력유기 상 변태, 구상화 등에 영향을 끼치고, G는 열로서 분산되는 에너지이다. 재료의 가공성을 극대화하기 위해서는 가해지는 에너지가 재료의 미세조직 변화에 소모되는 것이 유리하며 따라서 J이 높은 조건에서 소성변형하는 것이 유리하다고 할 수 있다. 에너지 분산효율 η는 주어진 조건에서의 J를 J의 최댓값(Jmax)으로 나눈 것으로 이를 식 (4)에 나타내었다[21].
에너지 분산효율 η는 일정 변형률에서 변형온도와 변형률 속도의 함수이며 해당 평면 위의 등고선(contour) 형태로 나타내어 최적의 에너지 분산 조건을 찾을 수 있다. 여기서 m은 변형속도민감도(strain rate sensitivity)이고 다음식 (5)과 같이 표현된다[21].
변형속도 민감도 m은 유동응력 곡선에서 기울기의 형태로 나타난다. 본 연구에서는 이들 관계곡선을 도시하는데 있어 다항식(polynomial equation)을 활용하여 기존의 단편적인 데이터 보다 연속적인 데이터를 얻고자 하였으며 이를 식 (6)에 나타내었다.
여기서 a, b, c, d는 다항식의 관계 계수로써 변형속도와 응력에 의존하는 상수이고 식 (5)와 식 (6)을 통해 변형속도민감도 m은 다음 식 (7)과 같이 나타낼 수 있다.
다항식을 활용하여 계산한 에너지 분산효율 η를 Fig 5에 나타내었다. 에너지 분산 효율 지도는 제품의 실제 변형량과 비슷한 압하율 60% 지점에서 도출하였고 Fig 5(a)와 Fig 5(b)는 각각 Φ40, Φ500 강재의 에너지 분산 효율을 나타낸 것이다. Φ40 강재는 온도조건 1050°C~1100°C 사이와 변형률 속도조건 1 × 10-1/sec~1 × 10-2/sec 사이에서 가장 높은 에너지 분산효율을 나타내었고, Φ500 강재는 온도조건 1100°C~1200°C 사이와 변형률 속도조건 1 × 10-1/sec~1 × 10-2/sec 사이에서 가장 높은 에너지 분산 효율을 나타내었다. 그리고, Φ40 강재에서 동적재결정에 의한 더 큰 연화현상에 의해 Φ500 강재 대비 다소 낮은 온도 공정조건에서 최대의 에너지 분산효율을 나타내었다.

Power dissipation efficiency map shown by temperature-log(strain rate) relatiopn (ε = 0.6); (a) Φ40 in diameter STS 321, (b) Φ500 in diameter STS 321.
동적재료모델의 에너지 분산효율을 통해 최적의 성형조건을 도출할 수 있으나, 성형 안정성을 평가하기에는 효과적이지 않기 때문에 본 연구에서는 Ziegler [22]에 의해 제안된 소성 불안정 기준(instability criterion)과 Malas와 Seetharaman 등[23]에 의해 제안된 4가지 기준 또한 함께 고려하였고 이를 식 (8)과 식 (9)에 나타내었다.
4가지 소성 안정 기준에서 m은 변형속도 민감도를 나타내고 s는 변형온도 민감도(deformation temperature sensitivity)를 나타낸다. 이들 안정 및 불안정 기준 역시 연속적인 data를 얻기 위해 다항식을 활용했고 Ziegler의 불안정 기준은 식 (7)과 식 (8)을 통해 다음 식 (10)과 같이 표현될 수 있다.
Malas와 Seetharaman 등의 4가지 안정기준 중에서 변형 속도 민감도 m에 의한 기준은 식 (7)을 통해 계산하였고 온도민감도 s는 응력-역 온도 곡선의 기울기에 의존적인 값이기 때문에 이들 역시 다항식을 활용하여 식 (11)과 같이 표현하였다.
여기서 a', b', c' 마찬가지로 다항식의 관계 계수이며 상수이다. 식 (11)을 통해 온도민감도 s는 다음 식 (12)와 같이 표현할 수 있다. 한편 s′은 변형속도 평면 위의 s의 기울기이기 때문에 s를 변형속도와의 다항관계식인 (13)과 같이 표현할 수 있다.
식 (13)의 a'', b'', c'', d'' 역시 다항식의 관계 계수이며 상수이다. 최종적으로 4가지 불안정 기준인 식 (9)는 식 (12)와 식 (13)을 통해 다음 식 (14)와 같이 표현될 수 있다.
식 (10)을 통해 특정할 수 있는 Ziegler의 소성 불안정 영역을 Fig 6에 나타내었다. 이들 지도 역시 마찬가지로 압하율 60% 지점에서 도출하였고 소성 변형 불안정 구간을 지도의 흰색 영역으로 나타내었다. Fig 6(a)는 Φ40 강재의 불안정 지도이며, Fig 6(b)는 Φ500 강재의 불안정 지도이다. Φ40 강재의 불안정 영역이 Φ500 강재의 불안정 영역보다 다양한 성형조건에서 나타남을 확인할 수 있다. 일반적으로 Ziegler의 불안정 구간은 상대적으로 빠른 변형속도, 낮은 온도 구간에서 나타나는데, Φ40 강재의 불안정 영역은 느린 변형속도, 높은 온도 조건에서도 나타난 반면에 Φ500 강재의 불안정 영역은 일관적으로 빠른 변형 속도 하에서 나타남을 확인할 수 있다. 이를 통해 STS 321 스테인리스강의 고온 변형에 있어 불안정 소성변형에는 변형속도의 영향이 더 크게 미치는 것을 알 수 있다.

Energy dissipation efficiency map shown by temperature-log(strain rate) relatiopn (ε = 0.6); (a) Φ40 STS 321, (b) Φ500 STS 321.
Malas 등에 의해 제안된 소성유동불안정기준 4가지를 Fig 7에 나타내었고 Ziegler의 불안정 지도와 마찬가지로 불안정 구간은 흰색 영역으로 나타내었다. Fig 7(a)는 Φ40 강재의 4가지 안정영역의 지도이고 Fig 7(b)는 Φ500 강재의 4가지 안정영역을 나타내고 있다. 이들 4가지 기준은 엔트로피 개념을 포함하고 있으며 m′과 s′ 조건이 가장 중요한 조건이다. m′ 불안정 영역은 두 강재 모두 아주 작은 국소부위에만 나타났고 이를 바탕으로 두 강 재의 고온압축실험에 있어서 변형 속도가 감소함에 따라 고온강도 값이 하락하는, 즉 더 적은 에너지로도 더 많은 변형을 일으키는 일반적인 고온변형거동을 나타내는 것을 확인할 수 있다. s′의 불안정 영역의 경우 Φ500 강재보다 Φ40 강재에서 더 넓고 다양한 위치에 나타남을 확인할 수 있으며 이를 통해 온도의 변화에 더욱 민감한 소재는 Φ40 강재임을 확인할 수 있다. 또한, 초기에 인가된 소성변형량의 차이에 의해 고온압축과정에서의 불안정성이 더 증가하기 때문에 소성유동 불안정 영역이 더 다양한 공정조건에서 나타나게 된다.

Deformation stability map shown by temperature-log(strain rate) relation of each STS 321 stainless steel (ε = 0.6); (a) Φ40 STS 321, (b) Φ500 STS 321.
Ziegler의 소성 불안정 기준과 Malas 등에 의해 제안된 소성유동불안정기준 4가지를 에너지 분산 효율 지도 위에 함께 나타낸 변형공정지도(Deformation Processing Map)을 Fig 8에 나타내었다. Fig 8(a)는 Φ40 강재의 변형공정지도이고 Fig 8(b)는 Φ500 강재의 변형공정지도이다. 각각의 지도에서 불안정 구간을 제외하고 에너지 분산효율이 높은 구간은 Φ40 강재의 경우 1050°C, 1 × 10-1~-2/sec 구간이고 Φ500 강재의 경우 1100°C~1200°C, 1 × 10-1~-2/sec 구간이다. 이들 구간의 미세조직을 변형공정지도와 함께 Fig 9와 Fig 10에 나타내었다. 이들 두 강재의 초기 결정립 크기는 큰 차이를 나타내었지만 변형공정지도상의 동일한 조건의 안정영역(Fig 9와 10의 1번 영역)에 이를 경우 최종적으로 비슷한 크기의 결정립 크기를 나타냄을 확인할 수 있다. Φ40 강재의 경우 1000°C 미만의 조건에서 압축을 진행한 시편에서 동적 재결정에 의한 결정립 미세화가 관찰되었으나 다수의 결함과 불균일하게 일어난 동적재결정을 통해 소성변형에 불안정한 구간임을 확인하였다.
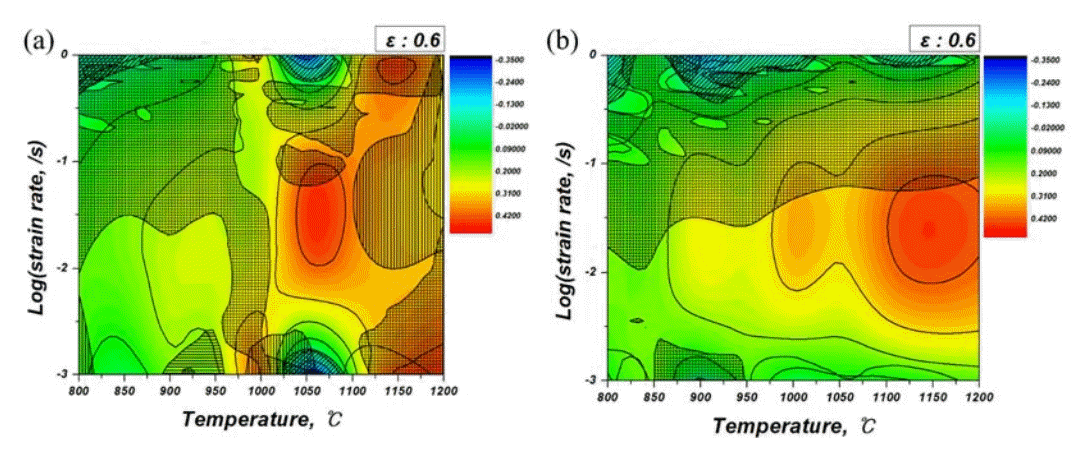
Complex processing map showing the stable and unstable deformation region (ε = 0.6). Slash region means the unstable region; (a) Φ40 STS 321, (b) Φ500 STS 321.
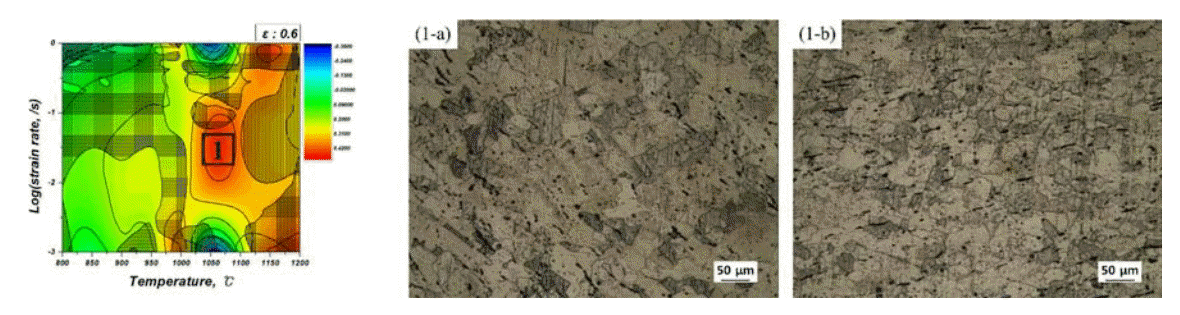
Microstructures on the processing map of Φ40 STS 321 stainless steel (1100°C, 1 × 10-2/sec condition).
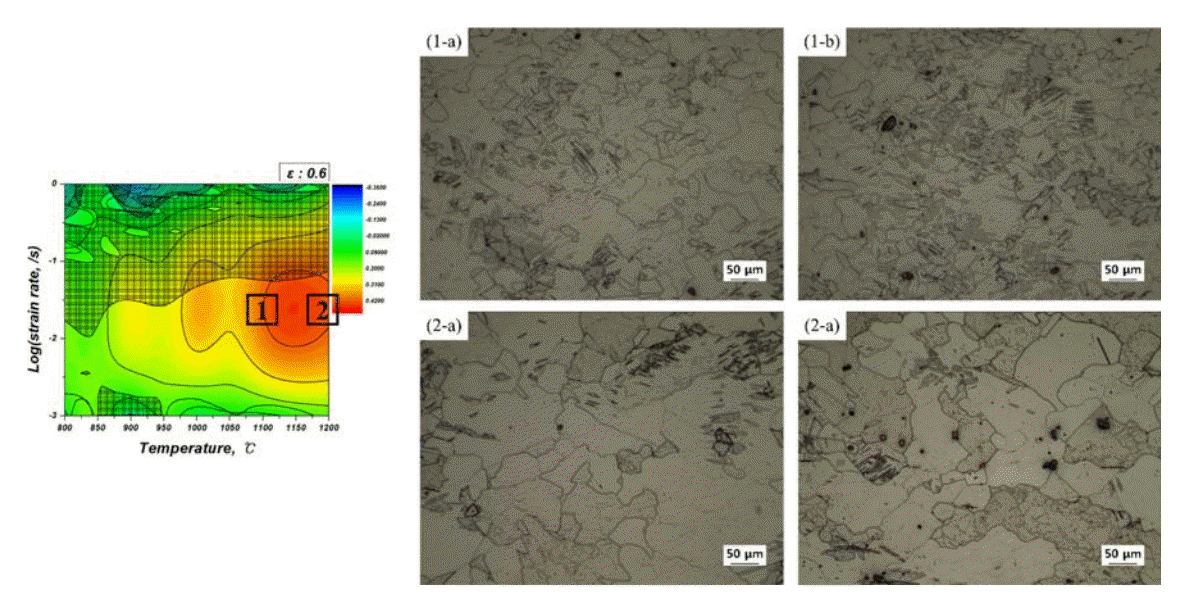
Microstructures on the processing map of Φ500 STS 321 stainless steel; (1) 1100°C, 1 × 10-2/sec condition, (2) 1200°C, 1 × 10-2/sec condition.
Φ500 강재의 경우 낮은 온도에서 압축 변형에 따른 불균일한 결정립 연신이 관찰되었고 1100°C, 1 × 10-2/sec 조건의 안정구역에서 결함이 줄어들고 결정립이 구상화 되었다. 그리고 같은 변형속도 조건의 다른 온도인 1200°C 조건의 미세조직을 관찰한 결과 결함이 없고 균일한 결정립을 관찰할 수 있으나 높은 온도로 인한 결정립 성장 또한 함께 관찰할 수 있었다. 재료의 고온변형공정에서 동적회복, 동적 재결정 등을 조절하는 것은 공정시 발생할 수 있는 불량뿐만 아니라 결정립 크기 또한 제어할 수 있으므로, 재료의 특성은 고온변형공정에서 대부분 결정되어진다[24-27]. 따라서 적절한 공정조건을 설정하여 결정립 크기 제어를 통한 물성제어와 결함의 제어가 고온 성형에 있어 가장 중요한 부분이라고 할 수 있다.
본 연구에서 고온압축실험과 그에 따른 변형공정지도를 도출하고 이를 미세조직과 연계 분석한 결과 압축 실험 후 비슷한 크기의 결정립을 나타내면서 안정구간이 넓게 나타나는 Φ500 강재가 고온소성변형에 있어 더 유리함을 확인할 수 있었다. 또한 그 조건으로 온도조건 1100°C, 변형속도 1 × 10-2/sec 조건이 성형에 있어 가장 유리할 것으로 판단된다.
4. 결 론
본 연구에서는 초기 미세조직의 차이가 STS 321 스테인리스강의 고온 성형성에 미치는 영향을 다항식들 적용한 동적재료모델을 활용하여 고찰하였으며, 다음과 같은 결론을 얻을 수 있었다.
1. 서로 다른 초기 미세조직을 가지는 STS 321 스테인리스강의 고온압축실험을 통해 각 소재의 평균 활성화 에너지(Q)를 구할 수 있었고, Φ40 강재의 경우 365.19 kJ/mol을 나타내었고 Φ500 강재의 경우 252.39 kJ/mol을 나타내었다. 또한 이들 열적활성화 에너지는 변형량이 증가함에 따라 그 값이 감소하여 일정 값에 수렴하는 경향을 나타내었는데, 이것은 일 에너지가 소성변형열로 전환됨에 따라 작은 활성화 에너지로도 소성변형이 가능하기 때문이다.
2. 초기 미세조직이 더 미세한 Φ40 강재가 Φ500 강재보다 소성 불안정 영역이 더 넓은 온도-변형속도 조건에서 나타나며 성형온도에 더욱 민감하고 결함 및 불균일한 동적 재결정 현상을 나타냈다.
3. 동적재료모델을 활용하여 온도와 변형속도에 따른 에너지 분산효율을 분석하였으며 소성불안정성을 확인하기 위하여 Ziegler의 기준과 Malas 등의 기준을 함께 고려하여 변형공정지도를 작성하였다. 또한 이를 미세조직과 연계하여 분석한 결과 Φ500 강재의 공정조건으로서 1100°C, 변형속도 1 × 10-2/sec 조건이 고온성형에 있어 가장 유리한 조건임을 확인하였다.
4. 고온 소성변형거동을 이해하고 변형공정지도를 활용함으로써 STS 321 스테인리스강의 고온 성형에 미치는 초기 미세조직이 끼치는 영향에 대해 고찰할 수 있었으며 이를 바탕으로 최적의 공정 조건을 도출할 수 있었다.
Acknowledgements
본 연구는 산업통상자원부 (MOTIE)와 한국산업기술평가관리원 (KEIT), 그리고 한국산업기술진흥원 (KIAT) 등의 연구지원으로 수행되었으며 (과제번호: 20013208, P0002019), 이에 감사드립니다.