이중 인공지능을 이용한 Al 7075 합금에서의 압광 균열 진단 연구
Diagnosis of Mechanoluminescent Crack Based on Double Deep Learning in Al 7075
Article information
Trans Abstract
The phenomenon of mechanoluminescence (ML) refers to the emission of light induced by mechanical stimulation applied to mechano-optical materials for example SrAl2O3:Eu,Dy (SAO). Numerous technologies on the basis of ML have been presented to visualize the stress or strain in various structures for the applications including structural health monitoring. As a result, extensive attention has been devoted to the design, synthesis, characteristics, optimizations, and applications of ML materials. However, challenges still remain in the standardization of ML measurement and evaluation, thereby commercially viable ML applications are currently unavailable. To overcome these difficulties, present study proposes ML measurement and evaluation techniques employing the ML fracture mechanics, finite element method, and dual deep learnings. For the effective normalization of visualized ML images under fixed initial ML intensity condition, continuous UV irradiation above the critical ML power density has been subjected to tensile and compact tension (CT) specimens. Therefore, Plastic Stress Intensity Factor (SIF) as well as crack tip stress field have been extracted successfully from normalized ML images based on ML fracture mechanics. To complement and verify the ML analysis, numerical FEM simulation and analytical ASTM calculation have been also provided. Finally, a double deep learning consists of Generative Adversarial Networks (GAN) and Convolutional Neural Networks (CNN) has been trained and tested for the standard evaluation of in-situ ML images.
1. 서 론
압광 현상 (Mechano-luminescence, ML) 은[1] 소재에 가해진 인장, 압축, 전단, 압력, 토크, 진동, 마찰, 파단 등과 같은 기계적 자극으로 인한 일종의 유도발광 현상이다. C.N. Xu 가 SrAl2O3: Eu2+(SAO) 소재에서 집중적이고 재현 가능한 ML 현상을 발견한 이후로[2], ML특성을 기반으로 하는 대상 구조물의 응력 또는 변형율을 시각화하기 위한 다양한 공학적 방법들이 시도되었다[3-23]. 이 결과로서, ML 재료의 설계, 합성, 특성 최적화, 및 그 기술 적용에 대한 주목할 만한 성과들이 보고되어 왔음은 주지의 사실이다[14,18]. 그럼에도 불구하고, ML 현상의 측정 및 평가 과정에 있어는 여전히 표준화과정에 다수의 난점들이 존재함으로 인하여, 현재까지 상업적으로 중요한 ML 기술의 응용은 극히 제한적으로 적용되고 있는 실정이다.
구체적으로는, 이론적인 측면에서, ML 발광 기구가 트랩 해제 공정 (Trap Release Process) 에[19] 지배됨으로써 트랩을 자극하는 하중 및 하중 속도에 이중적으로 반응하게 되며, 또한 실험적 측면에서도 구조물에 기계적인 응력이 작용되는 동안 적절한 가시광 방출을 포착하기 위해 강력한 사전 자외선 (Ultra Violet; UV) 여기 후 임의로 결정되는 완화 과정이 반드시 필요하게 된다[22,23]. 그 결과 구조물로부터 계측된 발광량 및 부가응력 사이의 상관관계를 해석함에 있어서, 복잡한 비 선형성, 2차 조화, 이력 거동, 및 보정되지 않은 ML의 초기 조건 특성 등을 모두 고려하지 않는 한 계측된 발광량의 유효응력 전환을 통한 구조물 상태의 정량분석이 완전히 불가능하게 된다[8,13,16,18].
따라서 본 연구에서는 기존의 누적 ML 계측 이미지를 사용하여 ML 발광량을 유효 응력의 항으로 전환하는 길고 복잡한 형태의 ML 역학 기반의 제한적인 표준화 과정을 배제하기 위하여 연속 UV 조사 조건하에서의 ML 응력 발광을 계측하고[14], 발광 가시화 영상으로부터 인공 지능을 기반으로 하는 유효응력 및 균열 첨단 부근의 특성 값을 직접적으로 산출할 수 있는 새로운 형태의 ML 표준화 분석 기법을 항공용 알루미늄 구조재의 건전성 평가에 적용해 보고자 하였다. 이를 위해, 적대적 생성 신경망 (Generative Adversarial Networks; GAN) [24,25] 및 합성곱 신경망 (convolutional neural network; CNN) [26,27]으로 구성된 이중 심층 신경망을 기존의 ML 역학적 방법에 의한 제한적 표준화 계산 소프트웨어에 통합함으로써 정량적으로 스케일링 된 ML 이미지에 따라 즉각적으로 2차원 유효 응력 패턴을 추출하고, 이를 기반으로 항공 구조물 안전성 평가를 가능케하는 ML 표준화 기술을 제시해 보고자 하였다. 기술적 측면에서는 구조물 안전진단의 목적으로 구축된 ML 하드웨어 및 인공 지능 소프트웨어를 통합적으로 검증하기 위해, 구조적 무결성을 모니터링 하는데 있어 가장 복잡하고, 민감하며, 어렵다고 알려진 알루미늄 금속 구조재의 균열 첨단부 응력장을 ML 발광 현상으로 가시화 후 유효응력의 항으로 추출하는 것이 가능한지, 또한 이를 기반으로 균열 첨단 부근의 위험도를 소성 응력 확대계수의 항으로 정량화 가능한지를 계측 및 평가 표준화의 관점에서 살펴보고자 하였다.
2. 실험 방법
2.1 시편 준비 및 실험장치 설정
본 연구에서는 Al 7075합금에 SAO 소재와 투 명 아크릴계 접착제를 혼합하여 제조한 ML 페인트를 도포함으로써, 구조용 7075 Al 합금 기지에 부가되는 응력으로부터 발생되는 ML 반응을 가시화 형태로 계측해 보고자 하였다.
이를 위해 SAO 파우더를 중량 비 30% 로 혼합 후 금속 틀을 활용하여 그림 1의 2 종 시험편 표면에 도포하였다. 시편의 형상은 ASTM E8, E399를 참고하여, ML Intensity와 응력 간의 관계를 알아보기 위한 인장 시험편과, 균열전파에 따른 균열길이 정량화 및 응력장 분포 등의 결과를 얻기 위한 CT시편을 각각 제작하였다. 기계적 시험은 만능 인장 시험기(Instron-5567)의 특수 설계된 로딩 스테이지에 시편을 장착 후 UV 램프(Innocure2000)를 사용하여 트랩 포화점에 도달하기에 충분한 시간인 5분 동안 시편에 UV를 노출하고, 크로스헤드 속도 0.05 mm/s. 에서 연속 UV 조사 조건을 적용하면서 수행하였다. 인장 및 파괴 과정의 가시화 평가를 위해서는 고속 카메라 (SA-X)를 사용하여 초당 60fps의 프레임 속도로 전체 파단 과정을 기록하였으며, 동시에 다중 채널 데이터 링크 (Multi Channel Data Link, MCDL)를 사용하여 카메라의 이미지와 만능 인장시험기로부터 얻어진 하중 및 변위 데이터를 동기화 하였다. 전체 실험 설정은 Fig 2에서 살펴볼 수 있다.

(a,d) Drawing drawn with reference to ASTM, (b,e) Real specimen with adhesive applied, (c) Metal frame for adhesive application
2.2 ML 역학 평가 및 FEM 모사
본 연구에서는 연속 U V 조사 조건하에서 계측된 인장 결과로부터 ML 발광량 및 유효응력 사이의 상관관계 구축하고, CT 시편의 파괴시험을 통해 균열 첨단 응력장의 위험도를 단일 파라메터 KPML의 항으로 자동 계산하기 위해 MatLab 소프트웨어를 이용하였다. 구체적으로 인장 시험의 고속 ML 이미지는 각 픽셀 좌표에 대한 정보를 포함하여 ML 강도의 표면 밝기 프로파일을 자동으로 추출하고 이를 인장시인장 시험기로부터 계측된 부가 응력 값과 대응 가능토록 하였다[3]. 또한 압광 파괴역학 기반하에서 CT 시험편으로부터 얻어진 영상의 처리를 통해 균열 첨단부 위치를 식별하고, 이를 중심으로 균열 첨단부 응력장을 추출함으로써 최종적으로 균열 위험도를 나타내는 KPML 값을 산출하도록 프로그래밍 하였다[8].
한편, 이중 심층 신경망 학습 데이터의 생성을 위해서는 파괴시험 결과에 대응되는 균열 전파 과정을 유한요소법 (Finite Element Method; FEM)에 기반한 Abaqus/CAE 6.13을 사용하여 모사하였다. 이때 3D 모델링 CT 시편은 Al 7075의 기계적 특성: E=71700MPa MPa v=0.33, σ0=535.435 MPa을 가지도록 설정되으며, 시뮬레이션 결과는 ML-MatLab 계산 결과의 검증에도 사용되었다.
2.3 이중 심층 신경망 학습
ML 발광 가시화 영상으로부터 인공 지능을 기반으로 하는 균열 첨단 응력장 및 응력확대계수값을 직접적으로 산출하기 위하여 그림 3 의이중 심층 신경망(GAN+CNN)이 도입되었다. 우선, https://github.com/phillipi/pix2pix [24]에서 제공되는 오픈 소스 코드에 기반하는 GAN은 Python (V3.6.6)에서 재구성되었다. 학습 및 시험용 데이터는 고속카메라에서 얻은 ML 이미지와 A BQU S 시뮬레이션으로 예측된 해당 FEM 이미지를 300 쌍 준비하였으며, 9:1의 비율로 분리 후 학습 및 평가에 사용하였다.
이후, 생성된 GAN 이미지로부터 소성응력확대 계수 값을 예측하는 CNN 모델은 MSE 손실 함수 및 Adam 옵티마이저를 기반으로 하는 5 개의 콘볼루션과 8 개의 MLP 레이어로 구성하였다. 그러나 GAN에 의해 생성된 가짜 ML 및 FEM 이미지의 소성 응력 강도 요소를 독립적으로 평가하기 위해 정방향 및 역방향 CNN이라는 두 개의 동일한 모델이 별도로 도입되었다. 전자는 시뮬레이션 된 FEM 이미지 및 KPFEM 값으로 훈련되었고, 후자는 실측된 ML 이미지 및 KPML 값을 사용하여 최적화되었다. 또한, 훈련된 CNN의 성능을 확인하기 위하여 상기 데이터 또한 9:1의 비율로 분리하여 응력확대계수 값의 학습과 평가에 사용하였다.
3. 결과 및 고찰
3.1 ML 역학기반 측정 및 평가
하중 부가 시 ML 여기의 초기 조건을 효과적으로 고정시킴으로써, 응력 제로 상태에서의 ML 영상이 보정된 표준 ML 이미지를 획득하기 위해, 본 연구에서는 임계 밀도 이상의 연속 UV 를 조사하는 조건 하에서 인장 및 파괴 시험을 진행하였다. 결과적으로 탄성 영역 내에서 단축 인장 시험에서 입증된 바와 같이[16], Fig 4 의 항복 응력까지의 인장 결과는 적용된 인장 응력과 순간적인 ML 강도 사이에 잘 정의된 선형 관계를 탄성역 및 소성역 구간 모두에서 보여주었다. 다만 소성역 대비 탄성역에서의 응력증가에 따른 밝기 증가가 극단적으로 적어 탄성응력의 변화를 가시화하기에는 상당한 어려움이 있을 것으로 판단되었다.
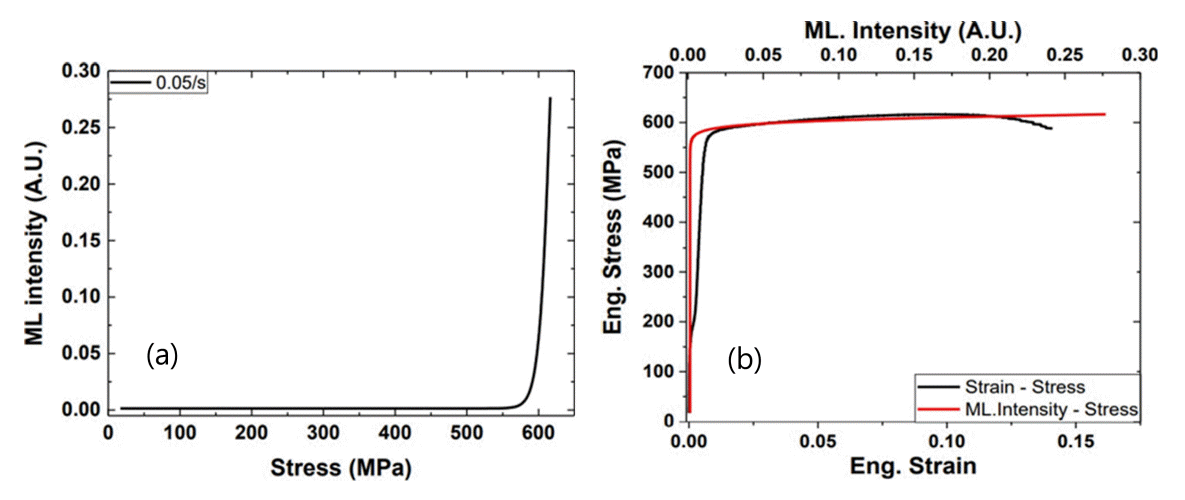
(a) ML intensity-stress and (b) ML intensity-stain relationship graph with tensile property of Al alloy
이러한 특성으로 인하여, 실제 Fig 5에서 살펴볼 수 있듯이, CT 시편을 이용한 균열 전파 상황에서의 균열 첨단부 응력 변화를 가시화하려는 시도에서 원거리 탄성역의 경우 계측이 거의 불가능하였다. 이는 ML을 통해 탄성 영역을 가시화할 수 있게 하려면 값비싸고 번거로운 강화된 카메라 시스템이 불가피하므로 ML 기술의 상업적 및 실증적 접근성이 심각하게 손상된다. 그러나 균열첨단 소성역의 경우 Fig 4에서 사전 예측한 것처럼 극도로 향상된 감도로 인하여 파괴 과정에서의 균열 첨단부 및 소성 응력 패턴을 Fig 5 (a,b)에서 성공적으로 검출할 수 있었다. 그 결과, ML 기술에 의해 계측된 소성 응력확대계수 값 KPML이 균열 팁과 균열 팁 근처의 순간 ML의 등가 강도 윤곽 패턴에서 주어진 프린지 루프의 가장 먼 지점 사이의 거리와, 균열 축에 대한 이 라인의 해당 경사각으로부터 성공적으로 계산될 수 있었다(그림 6). 또한 Fig 5 (c)에서 볼 수 있듯이 ML 의해 계측된 균열 팁 소성 영역의 크기와 ML 파괴역학에 기반하여 이론적으로 계산한 응력장의 패턴이 비교적 잘 일치하였다.

(a, b) Evolution of ML images with Crack tip and stress field predicted by Matlab Code and (c) their corresponding stress fields near the crack tip generated by FEM.
3.2 FEM 모사에 의한 검증 및 데이터 생성
본 연구에서는 ML 기반의 계측결과를 검증하고, GAN 및 CNN 훈련을 위한 일련의 데이터를 생성하기 위해 FEM 모사를 추가 도입하였다. FEM은 구조가 왜곡되는 위치를 상세하게 시각화하고 탄성 또는 소성 변형에 관계 없이 응력 및 변위의 분포를 나타낼 수 있다. 그 결과, Fig 6 및 5에서와과 같이 ML과 FEM 각각의 방법으로 도출된 KP 값과 함께 균열 팁 응력 패턴의 상호 비교가 가능해질 수 있다. 우선 균열 길이의 변화에 대해 ML 계측 및 분석 과정에 개입되는 실험편차 등의 영향으로 인하여 KPML의 변동 값들이 KPFEM보다 약간 더 낮게 계측되었지만, Fig 6의 KPML 및 KPFEM의 일반적인 경향 및 평균값은 비교적 수용가능한 수준의 일치를 보여주었다. 또한 그림 5의 균열 첨단 부의 소성역 패턴 또한 동등한 형태를 보여주었으며, 이로부터 ML 계측 기술이 비록 소성역에서의 변화만으로 한정되는 측면이 있으나 구조체에서의 파괴 양상을 정확히 계측할 수 있음을 알 수 있다. 마지막으로 FEM 모사 과정의 도입으로 시뮬레이션 결과에서 인공지능 학습용 데이터를 생성하는 시간이 크게 단축되어 학습 과정이 가속화되었다. 특히, FEM 소프트웨어는 기본적으로 시스템 모델링 및 분석의 복잡성을 제어하기 위한 광범위한 시뮬레이션 옵션을 제공하므로, 구조물 안전진단에서 요구되는 수준의 정확도를 가지는 학습 데이터의 생산이 단시간 내에 가능하였다.
3.3 GAN 및 CNN 모델 평가
전술한 ML 기반 구조물 진단 기술은, 연속 U V 조사 조건을 적용함으로써, ML 여기의 초기 조건을 효과적으로 고정시켜, 실제 구조물 모니터링 상태 하에서 전파하는 균열 소성부를 실시간으로 감지하고 평가함에 있어 표준화에 대한 가능성을 제시하였다. 그러나, 복잡하고 다양한 실 구조물 측정 시 발생되는 재료, 계측, 및 측정 요소의 변화를 일관되게 동기화하고 이를 기반으로 해석의 엄밀성을 유지하는 것은 매우 어려우며, 위에서 제시한 연속 U V 조사 조건만으로 다양한 다중 스케일 구조물들의 안정성 분석에 완벽하게 적용할 수는 없다. 따라서 본 연구에서는 새로운 대안적인 방법으로 GAN과 CNN으로 구성된 이중 인공을 이용하여, ML 사진과 시뮬레이션 된 FEM 이미지를 재귀적으로 동기화하고 학습함으로써, ML 계측 값의 실시간 표준분석 가능성을 타진해 보았다.
다시 말해, 상술한 이중 인공지능 기반의 ML 표준화 시스템은 각각 ML 및 FEM 2개의 통상적 측정 및 검증 경로 외에 GAN 및 CNN으로 구성된 AI 분석 경로를 포함한다. ML 파괴 역학은 일반적으로 구조 상태에서 균열의 중요성을 알리기 위해 단순화된 단일 매개 변수인 소성응력 강도 계수(PSIF: KPML)를 사용하여 균열 팁과 첨단부 응력 패턴을 함께 제공한다. 반면에 FEM 계산은 시뮬레이션으로 균열 전파 동안 동일한 상황에서 가시화된 ML 균열 팁 응력 영역과 KPFEM 값을 검증한다. 한편, 기존 ML 및 FEM을 대체하는 이중 AI 경로는 잘 훈련된 GAN을 사용하여 측정된 ML 또는 시뮬레이션 된 FEM 이미지에서 AI로 변환된 FEM 또는 ML 이미지를 그림 7에서와 같이 생성하고 이렇게 생성된 가짜 이미지들은 CNN 모델을 통하여 그림 8의 KPAI 값을 구할 수 있었다. 여기서 GAN의 양방향 및 대화식 구조는 두 네트워크 모두에 적용되어 생성기가 더 나은 이미지를 생성하는 동시에 판별기가 합성 이미지를 표시하는 데 능숙하게 만들어 주었다. 따라서 GAN은 Fig 7과 같이 관찰자에게 거의 사실적으로 보이는 가짜 ML 및 FEM 사진을 즉각적으로 생성할 수 있었다. 또한, 이로부터 CNN에 의해 예측된 KPAI·ML&AI·FEM 값의 크기는 각각의 실험 및 시뮬레이션 된 KPML&FEM의 값과 적절히 일치함을 보여주었다.
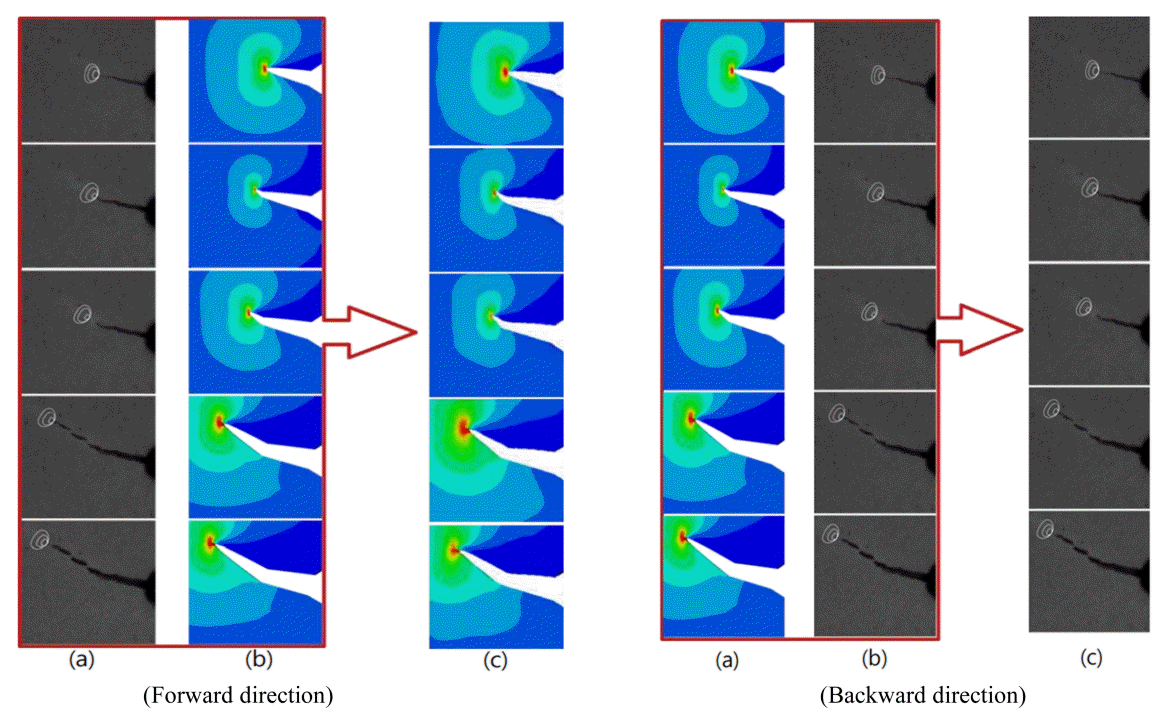
Comparison of real images and fake images generated using GAN (a), (b) real ML and FEM images, (c) generated fake FEM(forward) and ML(backward) images
다만, 그림 8에서 살펴볼 수 있듯이 예측된 KPAI·ML&AI·FEM 값의 오차는 정방향 및 역방향 모두 학습률 98% 이상의 수준에서, ASTM 방법에 의해 계측된 KPASTM 값 대비 각각 13% 및 3% 를 나타내었다. 이는 본 연구에서 제안하는 정방향의 학습된 인공지능이 실측 ML 영상으로부터 ASTM 표준계측 방법이나 FEM 연산에 의해 예측된 값과 거의 일치하는 매우 높은 정밀도의 안전진단을 가능케 한다는 것을 의미한다. 그러나 GAN 에 의해 학습된 역방향의 계측 값 검증을 위한 FEM 연산 결과로부터 예측된 값이 13 % 의 상대적으로 높은 오차 값을 보임으로써 향후 이에 대한 보완 연구가 필요한 것으로 판단된다.
4. 요 약
SAO 계 ML 소재에서 GAN과 CNN으로 구성된 이중 인공 지능의 도움으로 ML 측정 및 평가의 표준화를 위한 새로운 혁신적인 개념이 제안되었다. 기존의 ML 및 FEM 기술은 ML의 표준화를 보완할 뿐 아니라 GAN 및 CNN 훈련을 위한 데이터 세트를 효과적으로 생성할 수 있었다. 기술적으로, ML 전력 밀도 이상의 연속 UV 광 여기는 ML 여기의 초기 조건을 고정함으로써 일련의 보정된 표준 ML 이미지를 손쉽게 획득할 수 있게 하였다.
또한, CT시험에서의 ML 및 균열 팁 부근의 해당 소성응력 강도 계수 (SIF)는 ML 역학 및 양방향 머신 러닝의 두 가지 기준을 사용하여 평가되었다. ML 역학을 기반으로 하는 새로운 MatLab 연산 결과는 소성 균열 팁, 강도 윤곽 패턴 및 KPML에 해당하는 최대 ML 강도 위치를 성공적으로 식별했다. ML 역학에 의해 이론적으로 예측된 균열 팁 응력 영역의 크기와 모양은 ML 강도로부터 KPML 의 결정에 사용된 실험 ML 등변색 패턴과 잘 일치하였다.
마지막으로, 정 방향 및 역방향 GAN은 관찰자에게 거의 실제처럼 보이는 가짜 FEM 및 ML 이미지를 성공적으로 생성할 수 있었으며, CNN은 소성 SIF를 높은 정밀도로 추정할 수 있었다. 특히, 이 값들은 ASTM, ML 역학 및 FEM에 의한 측정 및 모사 값과 비교적 잘 일치하였다.
Acknowledgements
This work was supported by a National Research Foundation of Korea grant funded by the Korean government (MPIS) [2021R1A2C1005732], Fundamental & Public Facility Building Research to Activate Industry Funding by the Ministry of Science and ICT [POC3330], and Internal Project of Korea Institute of Materials Science supported by NST [PKC2034].