Sputtering공정 적용 Ag-Ti 조성경사형 박막의 구조분석
Study on Ag-Ti Thin Film Structure with Compositional Gradient Fabricated by Sputtering Process
Article information
Trans Abstract
In this study, a composition-gradient thin film was applied for the formation of intermediate layer of Ti seed layer for an stable electrode stack Ag metal layer. Various composition of Ag-Ti hetero metal layer were simultaneously deposited by using the sputtering process with Ti and Ag target, respectively. An intermediate layer was deposited at a gradient composition ratio such as 5:5 and 7:3. In addition, the optimal deposition conditions were evaluated by confirming the plasma codition such as density of plasma ion, plasma potential with the Langmuir Probe (Hiden ESPion). Flow rate, power, and composition ratio were optimized as variables for thin film structures of compositional gradient thin films. In addition, thin film samples were heat treated at 200 °C, 300 °C, and 400 °C to relieve the residual stress between the interface of laminated thin films. Under these conditions, a composition-gradient thin film was evaluated by XRD (X-Ray Diffraction, SmartLab Rigaku 9kW), SEM (Scanning Electron Microscope, Nova NanoSEM 450), and EDS (energy dispersive X-ray spectroscopy). As a result of the measurement, it was confirmed that interfacial diffusion occurred due to the composition gradient thin film. When the composition gradient intermediate layer was applied to thin film stack, the residual stress increased more than that of single thin film stack. However, after stress relief annealing, residual stress was dramatically decreased compared to single stack.
1. 서 론
박막 증착 기술은 반도체, 태양 전지, 광학, 센서 등 다양한 공학 분야에서 사용되며 Sputtering 공정은 박막 증착에서 가장 널리 사용되는 공정이다. Sputtering은 고에너지 입자 충돌로 인해 타겟 표면에서 기판으로 물질이 증착되는 것으로 다양한 공정 조건에서 박막의 구조 및 특성이 변한다. 박막으로 금속을 증착할 때 금속과 기판의 표면에너지 및 결정 결합 상태가 잘 맞지 않으면 박리현상과 같은 현상이 일어나는데 이러한 문제를 방지하기 위하여 Seed layer를 기판과 박막 사이에 증착한다[1]. 이러한 Seed layer는 전극 층과는 다른 금속을 사용하여 이런 금속 간의 물리적, 전기적 특성 차이를 완화하기 위하여 중간층으로 조성경사형 박막을 증착하였다.
본 연구에서는 Sputtering 공정을 사용하여 Ti금속의 Seed layer와 Ag금속의 전극 층 그리고 Ag-Ti이종금속을 동시에 증착하는 조성경사형 박막을 중간층으로 사용하였다. 조성경사형 박막은 증착 파워를 150W 기준으로 Ti:Ag가 3:7, 5:5, 7:3가 되도록 증착하여 박막층 내의 Ti와 Ag의 조성이 경사형이 되도록 증착하였다. 이러한 Sputtering공정에서 최적의 유량조건을 탐색하기위하여 Langmuir Probe(Hiden ESpion)를 사용하였고 단일 탐침법 플라즈마 측정으로 조건에 따른 플라즈마의 특성상태를 확인하여 최적의 증착조건을 고찰하였다. 플라즈마 측정조건은 유량과 파워의 변화를 두었고 유량은 20sccm, 40sccm, 60sccm, 80sccm로 파워는 DC-RF동시파워 150W로 설정하였다.
조성경사형 박막의 최적화를 위한 실험조건으로는 증착 파워의 비율, 유량, 증착시간과 더불어 열처리온도를 변수로 설정하였다. 유량은 플라즈마 측정을 통하여 찾은 최적 조건인 40sccm으로 설정하였고 파워는 DC-RF동시파워 50W, 100W, 150W로 그리고 증착시간은 5min으로 설정하였다. 또한 적층박막 간의 잔류응력 해소를 위한 열처리박막 조건은 200 °C, 300 °C, 400 °C로 설정하였다. 이러한 조건으로 조성경사형 박막과 조성경사형 박막을 적용한 적층 박막을 제작하여 XRD(X-Ray Diffraction, SmartLab Rigaku 9 kW), SEM(Scanning Electron Microscope, Nova NanoSEM 450), EDS(energy dispersive X-ray spectroscopy)를 사용하여 특성 평가를 진행하였다[2-3].
2. 실험 방법
2.1 Langmuir Probe를 사용한 플라즈마 측정
본 실험에서는 플라즈마의 거동을 확인하고 최적의 증착 조건을 연구하기 위하여 Langmuir Probe를 사용하여 플라즈마를 측정하였다. Langmuir Probe는 단일 탐침법으로 플라즈마에 충돌된 전자가 탐침으로 포집되며 이러한 전자의 데이터로 전자의 밀도, 온도, 전기장의 측정이 가능하다[4].
박막공정 시 최적의 유량 조건을 확인하기 위하여 Langmuir Probe를 사용해 플라즈마의 거동을 측정하였고 전자밀도, 플라즈마 포텐셜, 이온 플럭스 등의 데이터를 통하여 최적의 플라즈마 조건을 확인하였다. 파워조건은 150W에 RF-DC 동시파워를 사용하였고 유량조건은 20sccm, 40sccm, 60sccm, 80sccm으로 설정하였다. 이러한 조건으로 플라즈마를 측정하였고 측정 데이터를 I-V곡선과 전자에너지 분포함수(EEDF)를 통하여 분석하였다.
2.2 박막증착 실험
최적의 조성경사형 박막과 적층조건을 탐색하기 위하여 조성경사형 박막을 조건별로 증착하였고 그림 1과 같은 구조와 공정 방식으로 조성경사형 적층 박막을 증착하였다. Sputtering공정 시 파워조건을 변수로 두었고 Ag layer와 Ti layer는 50W, 100W, 150W의 조건으로 증착을 진행하였다. 또한 조성경사형층은 Ag:Ti 기준 조성비 7:3, 5:5, 3:7으로 증착조건을 설정하여 각각 150 W:50 W, 100W:100W, 50W:150W로 증착공정을 진행하였다. 조성 경사형을 적용한 적층박막은 Ti금속을 Seed Layer로 150W, 5 min 증착하고 조성비 7:3, 5:5, 3:7의 비율로 5 min씩 증착한 조성경사형 박막을 중간층으로 적층한 후, 전극층으로 Ag금속을 150W, 5 min 적층하였다. 유량은 Langmuir Probe를 사용한 플라즈마 측정결과에서 가장 우수한 특성을 보인 40sccm을 설정하였고 증착시간은 5 min으로 설정하였다. 이러한 조건으로 만든 샘플을 XRD와 EDS를 통하여 측정하고 결과를 통하여 면간거리, 결정크기, 잔류응력을 계산하여 분석하였다[5-6].
2.3 조성경사형 박막 열처리
박막적층 시 두 가지의 다른 금속박막을 적층하게 되면 서로 다른 물리적 특성으로 인하여 잔류응력이 높아지게 되고, 조성경사형 박막을 사용하여 잔류응력을 완화하지만 남아있는 잔류응력 해소와 박막계면에서의 금속 간 확산을 위하여 온도조건에 따른 열처리를 진행하였다. 온도조건은 표 2와 같이 Ag:Ti를 5:5의 비율로 150W, 5 min 증착한 샘플을 200 °C, 300 °C, 400 °C로 열처리를 진행하였다.
3. 결과 및 고찰
3.1 Langmuir Probe 분석
박막증착 공정 시 최적의 유량조건을 탐색하기위해 Langmuir Probe를 사용하여 플라즈마 측정을 진행하였다. 150W의 RF-DC 동시파워를 사용하였고 유량조건은 20sccm, 40sccm, 60sccm, 80sccm로 설정하였다. 그림 2는 플라즈마 측정결과를 I -V곡선으로 나타낸 그래프로 전위구간은 비슷하게 측정되었고 80sccm에서 가장 높은 전류와 포화구간이 측정되었고 구형탐침(spherical probe)의 형태가 확인되었다. 그리고 20sccm과 40sccm에서 전류는 낮지만 안정적인 원형탐침(cylindrical probe)의 형태가 나타났다. 또한 그림 2의 I -V곡선, EEDF그래프를 분석해볼 때 40sccm에서 안정적인 에너지 분포도와 전자 포화도가 측정되었다[7,8].
3.2 조성경사형박막을 사용한 적층박막의 SEM, EDS 분석
조성경사형 박막층이 중간층으로 적층되었을 경우 일어나는 현상을 관찰하기 위하여 적층된 박막을 400 °C에서 1시간 열처리한 후, 단면을 SEM과 EDS로 측정하였다. 그림 3은 Si wafer위에 조성경사형 박막을 중간층으로 사용한 Ag-Ti 적층박막의 단면과 단일 박막층의 Ag, Ti, Ag-Ti-5:5 단일박막의 단면을 측정한 SEM결과이다. (a)는 Ti금속박막, (b)는 Ag-Ti-5:5 조성경사형 박막 (c)는 Ag금속박막을 볼 수 있다. (d)는 조성경사형 중간층을 적용한 Ag-Ti 적층박막으로, 다른 조건에 비하여 박막구조가 균일하고 조밀하게 적층된 것을 확인할 수 있다.
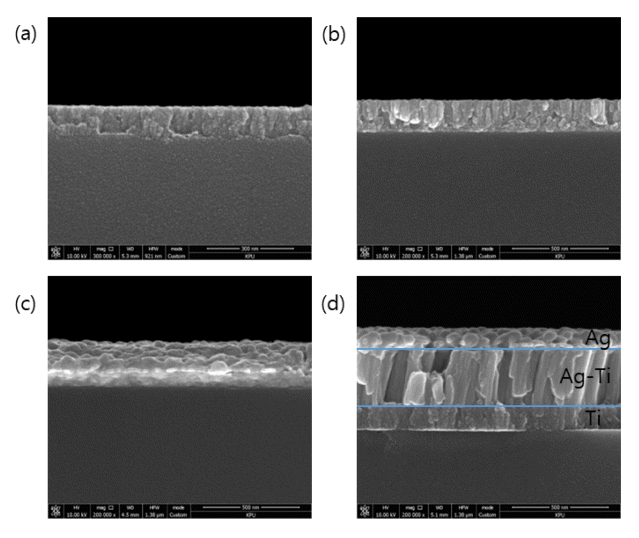
SEM results according to the thin film layer. (a)Ti layer, (b)Gradient compostion Ag-Ti hetero-layer (c)Ag layer, (d)Ag-Ti la minated film with gradient composition layer
표 3은 열처리된 적층박막의 EDS결과로 (1)Ti층의 표면의 조성은 38.1 wt%로 Ag가 확산되었으나 61.8 wt%로 Ti가 가장 높은 것으로 확인되었고 (2)조성경사형 층은 Ag 59.5 wt%와 Ti 40.4 wt%로 나타났다. (3)Ag층에서 조성경사형층과 가까운 표면부분은 Ti가 25.1 wt%로 검출되었고 Ag가 74.8 wt%로 확인되었다. 이는 Sputtering 공정과 고온열처리를 진행함에 따라, 각 적층간의 계면에서 상호고용과 확산이 일어났기 때문으로 판단된다.
3.3 박막공정 파워, 조성비 조건에 따른 XRD 분석
그림 4에 Ag:Ti를 증착파워비율 7:3, 5:5, 3:7로 5min 증착한 샘플의 XRD 분석결과를 나타내었다. 파워에 따른 XRD 결과는 Ag의 (111)Main peak의 위치와 반가 폭의 변화로부터 면간거리와 격자변형의 정도를 측정하였다. 전체적으로 비슷한 면간거리와 격자변형의 경향을 살펴볼 수 있었고, 특히 7:3과 5:5 비율 조건에서는 비슷한 peak 강도와 0.176, 0.175로 비슷한 격자 변형이 측정되었다. 또한 3:7에서 강도가 높은 peak이 나왔으며 격자변형이 0.137로 가장 낮은 값을 보여주고 있다. 이는 증착 파워 비율 3:7의 경우가, Ag-Ti의 상호고용 효과가 가장 안정적이기 때문으로 사료된다.

XRD and lattice strain results according to gradient composition ratio. (a)XRD graph (b)Lattice strain graph
그림 5는 50W, 100W, 150 W 증착파워를 사용하여, Ag:Ti를 같은 파워 비율로 설정하고, 5 min 증착한 샘플을 비교한 그래프이다. 75W에서 0.367로 가장 높은 격자변형과 0.237 nm의 높은 면간거리가 측정되었고 150W에서 가장 높은 강도의 peak과, 가장 낮은 격자변형이 0.193이 측정되었다. 이러한 결과로 150W가 가장 최적화된 결정성을 가진 조성경사형 박막 조건으로 판단된다[9-11].
3.4 조성경사형 박막의 열처리조건에 따른 XRD 분석
열처리 조건에 사용된 샘플은 150W기준 Ag:Ti가 5:5로 파워로 5 min증착되었고 잔류응력을 해소하기 위한 열처리 온도조건은 200 °C, 300 °C, 400 °C로 설정하였다. 또한 조성경사형 중간층을 적용하지 않은 단일막 Ag-Ti 적층 샘플은 150W에서 각각 Ag, Ti단일박막을 5min씩 증착하였다. 조성경사형 적층박막을 적용한 샘플은 150W로 Ti 5 min 증착 후 7:3, 5:5, 3:7을 각각 5min 증착하고 Ag 5 min 증착한 샘플을 사용하였다[12-14].
그림 6은 150W기준 5:5로 증착된 샘플을 200 °C, 300 °C, 400 °C로 열처리한 샘플로 전체적으로 모든 온도에서 낮은 격자변형이 측정되었고 400 °C에서 0.0377의 가장 낮은 격자변형이 측정되었다. 또한 Main peak의 비율이 달라진 것으로 보아 열처리 중 Ag:Ti 두 금속 간에 확산이 일어난 것으로 보인다.

XRD and lattice strain results according to annealing temperature. (a)XRD graph (b)Lattice strain graph
그림 7은 150W에서 각각 Ag, Ti 단일박막을 5min씩 적층한 샘플과 Ti를 5 min증착 후 조성경사형 박막을 3:7, 5:5, 7:3비율로 각5 min 증착하고 Ag를 5 min 증착한 적층 샘플을 400 °C에서 열처리한 것으로 격자변형이 줄어든 것을 확인 할 수 있었다. Ag-Ti 적층박막 샘플의 경우 격자변형이 0.225에서 0.171로 줄어드는 것을 확인할 수 있었고 결정 사이즈가 17.25 nm에서 22.65 nm로 성장하였다. 조성경사형 적층박막 샘플의 경우 격자변형이 0.243에서 0.158로 줄어드는 것을 확인 하였고 결정 사이즈가 15.97 nm에서 24.49 nm로 성장하는 것을 확인하였다.
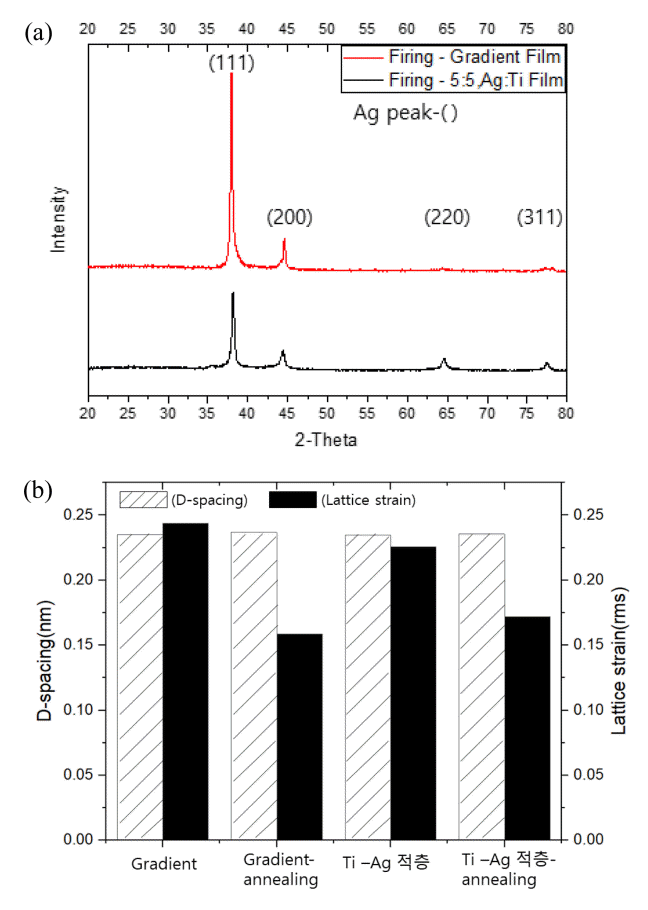
XRD and residual stress results of Ag-Ti stacked thin films and stacked thin films applied with composition gradient layer. (a)XRD graph (b)Lattice strain graph
열처리하기 전 샘플의 XRD는 조성경사형 적층박막의 peak이 Ag-Ti 적층박막 보다 더 낮았으나 열처리 후에는 조성경사형 적층박막이 더 높은 강도의 peak이 나왔고 조성경사형 적층박막의 격자변형이 0.243으로 0.225인 Ag-Ti 적층박막보다 더 높았으나 열처리 후에는 0.158과 0.171로 더 낮은 격자변형이 나타났다. 또한 조성경사형 적층박막을 적용한 구조가 조성경사형을 사용하지 않은 박막에 비해 잔류응력이 높았으나 열처리로 인하여 조성경사형 중간층을 적용한 박막은 35%, Ag-Ti 적층박막은 24%로 조성경사형 박막구조의 경우가 더 높은 폭으로 응력 해소가 되었다.
4. 결 론
본 연구에서는 두 가지 금속을 Sputtering공정으로 증착할 때 중간층을 조성경사형 박막으로 사용하여 적층된 박막의 특성차이를 개선하였다.
조성경사형 박막을 적용한 적층박막은 150W에서 Ti를 5 min증착하고 Ti:Ag를 3:7, 5:5, 7:3비율로 동시증착 그리고 Ag를 5 min 증착하여 만들었다. Sputtering을 사용한 조성경사형 박막증착 시 증착조건은 증착 파워를 RF-DC 동시파워를 동시에 사용하였고 50W, 100W, 150W를 각각 5:5의 비율로 나누어 증착을 진행하였다. 또한 150W 기준으로 RF:DC 파워를 7:3, 5:5, 3:7의 조성비로 증착하여 면간거리와 잔류응력을 계산하였다. 조성비에 따른 XRD 측정 결과로부터, 3:7, 5:5, 7:3모두 비슷한 잔류응력과 면간거리가 측정되었고 파워에 따른 결과는 150W에서 가장 낮은 0.193의 잔류응력이 측정되었다. 또한 열처리를 한 적층박막 조건은 400 °C에서 가장 낮은 0.158의 잔류응력이 측정되었다. 조성경사형 중간층이 적층된 Ag-Ti 다층 박막과 Ti 단일막, Ag단일막 적층 샘플을 열처리 했을경우 조성경사형이 적용된 적층박막이 11% 더 높은 감소폭의 변화를 보였다.
즉 조성경사형 박막을 단일 박막 사이의 중간층으로 적용하였을 경우, 적층된 Ag, Ti박막의 잔류응력과 Ag, Ti박막간의 금속입자 확산으로 박리현상과 같은 물리적 특성이 개선되었고 면간거리의 확장과 Ag, Ti금속입자 간 확산으로 Ag, Ti박막 간에 전기적 특성차이가 개선되는 효과를 확인하였다.
Acknowledgements
이 논문은 산업통상자원부의 소재부품 기술개발사업 “글로벌 통신사업자 5G RF Component 개발’’의 지원과 2017년도 정부(교육과학기술부)의 재원으로 하는 한국연구재단의 대학중점연구소 지원사업으로 수행된 연구결과임(Grant No. 20016657)(NRF-2017R1A6A1A03015562).